フォームへの入力ありがとうございました。全文をお読みいただけます。
2D・3D図面から製造不具合や顧客クレームなど、価値ある関連情報を素早く検索・表示する方法
皆さん、こんにちは。本日はご参加いただき、ありがとうございます。
では早速、本日のスピーカーをご紹介いたします。株式会社ミラリンクから、高浪さん、田中さん、近藤さんの3名に登壇いただいております。まずは高浪さん、お願いします。
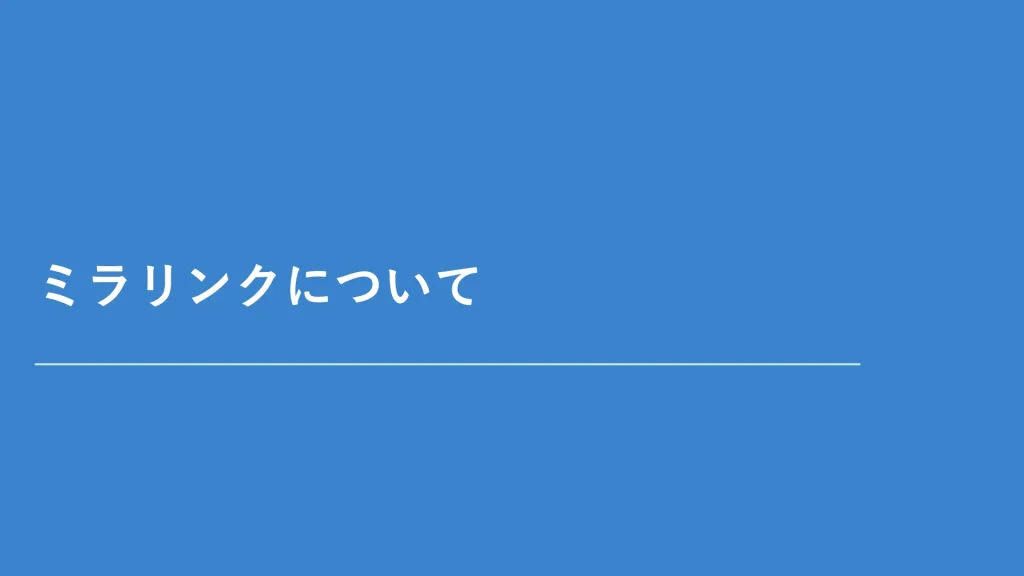
改めまして、本日はお忙しい中、セミナーにご参加いただき誠にありがとうございます。
株式会社ミラリンクのマーケティングを担当しております高浪と申します。
本日は「開発部門内に存在するノウハウをすぐ見つける—設計ナレッジ共有の最前線」というタイトルでお話をさせていただきます。
製造業界では、技術の進化やデジタル化が進む一方で、現場に残るノウハウがいまだにうまく活用されていないという課題があります。皆様もプロジェクトを進める中で、必要なデータや過去の事例を探し出すのに時間がかかって苦労した経験はあるのではないでしょうか。
本日のウェビナーでは、そういった設計現場の課題に対して、ミラリンクがどのように解決策を提供できるのかお話しさせていただきます。今日のセミナーをお聞きになって、皆様の業務の中で参考になる部分がありましたら幸いでございます。
本日のセミナーの流れについてご説明いたします。まず私、高浪から弊社ミラリンクの紹介と製造業の一般的な課題、そしてその解決方法についてお話しいたします。続いて、技術営業の田中が設計者向けのナレッジ活用例をご説明します。最後に、エンジニアの近藤がデモンストレーションを行う予定です。
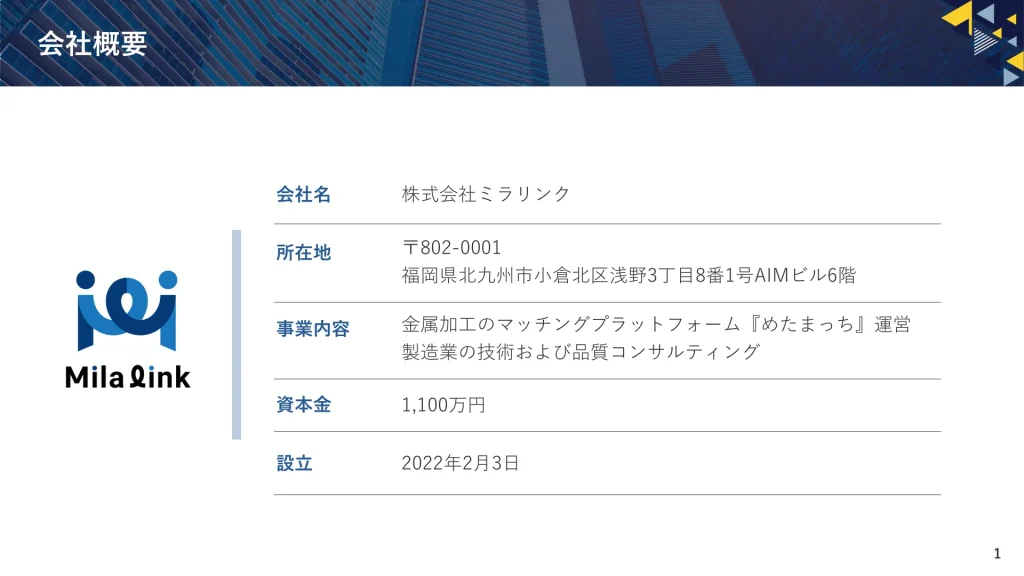
それでは、まずはミラリンクという会社のご紹介から簡単にさせていただければと思います。
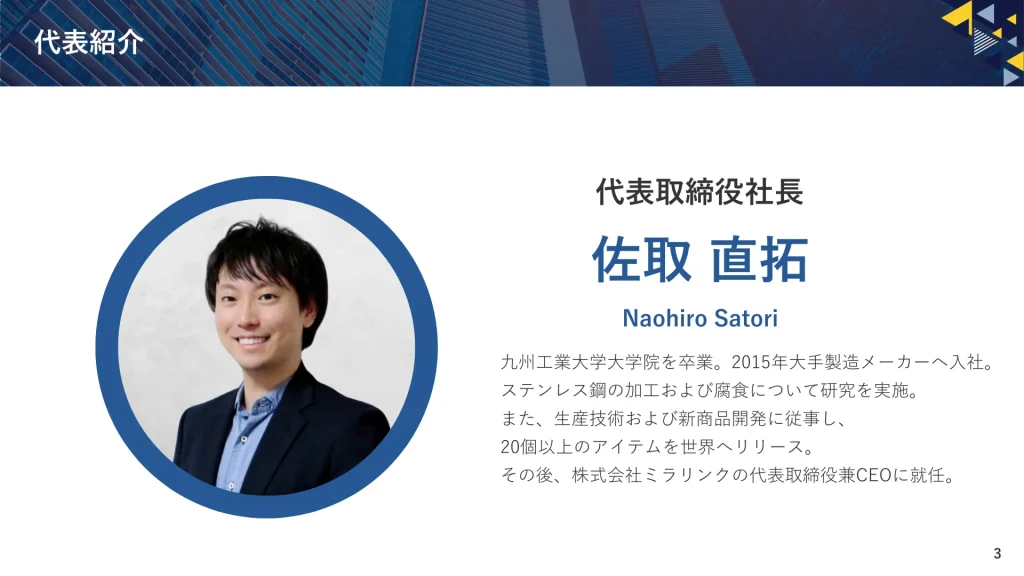
弊社ミラリンクは、製造業に特化したソリューションを提供している、福岡に拠点を置く会社です。この後詳しくお話しいたしますが、事業内容としましては、製造業向けの金属加工のマッチングプラットフォーム「めたまっち」の運営や、ものづくりのコンサルティングサービスを行っております。
代表の佐取は大手製造メーカーで新製品開発に携わっていた経験があり、約20個のアイテムを世界にリリースしてきました。実際の開発現場の中で「こういう仕組みがあったらいいのに」「こうすればもっと便利になるのに」と日々感じていた思いを形にするため、株式会社ミラリンクを立ち上げました。
ミラリンクは「誰もが自由にものづくりできる世界を実現する」というビジョンを掲げ、製造業の課題解決に日々情熱を注いでいます。人手不足やIT活用の遅れなど、製造業の課題を私たちは「自由なものづくりの壁」と表現し、その壁をAIやデジタル技術を駆使して打破していくことがミラリンクの使命であると考えています。
次に、事業内容について。ミラリンクでは現在、主に以下3つのサービスを展開しております。
- 金属加工のマッチングプラットフォーム
「めたまっち」 金属加工の依頼をしたい企業様と工場をつなぐことで、ものづくり業界の発展と新商品開発の支援をいたします。発注者であるメーカーは画面に沿って依頼内容を簡単に入力するだけで、すぐに一括見積もりをすることができます。金属加工に特化しているという点が一番の特徴で、金属加工に特化した工場が現在250社以上ご登録がございます。用途としては量産が約3割、製品の試作が7割で、案件成約率は約80%と、マッチングプラットフォームの中では比較的高い成約率を維持しています。 - ものづくりコンサルティングサービス
こちらは「めたまっち」と併用してご利用いただくケースが多いのですが、「製品を作りたいけど設計者がいないのでどう進めたらいいのかわからない」という会社様や、「外部に依頼して設計者の業務負担を少しでも軽減したい」といった課題をお持ちの企業様に対して、現場経験豊富なサポーターが技術的な課題の洗い出しや素材の選定など、一緒に伴走しながらものづくりを進めていくサービスです。 - 設計者向けノウハウ活用システム
今回主にお話しさせていただくシステムになりますが、こちらは設計開発担当者の業務効率をアップさせる設計サポートシステムです。このシステムは、設計開発の現場におけるノウハウや技術データの検索、活用を効率的に行うことを目的としたシステムです。この後のセッション後半でもう少し詳しく紹介いたします。
まずは、昨今の製造業を取り巻く課題についてデータを用いてお話しいたします。
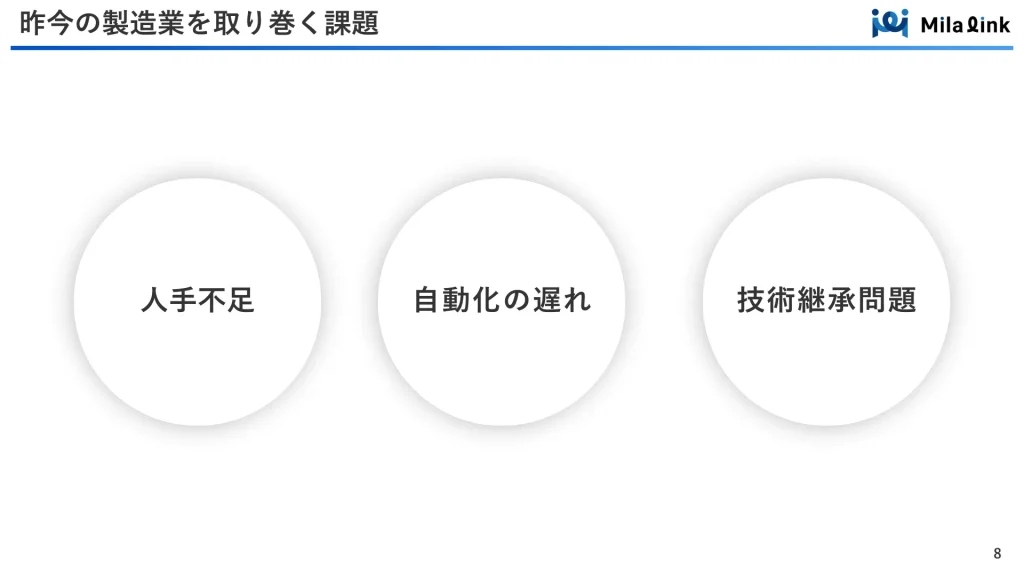
製造業は今、様々な課題に直面しています。
新型コロナウイルスの感染拡大や世界的な半導体不足など、日本の製造業を取り巻く環境はここ数年で大きく変化する中、さらに多くの問題が顕在化しつつあります。
人手不足、自動化の遅れ、技術継承問題といった課題があり、これらが相互に影響し合って製造業の現場に大きな負担をかけていると考えています。
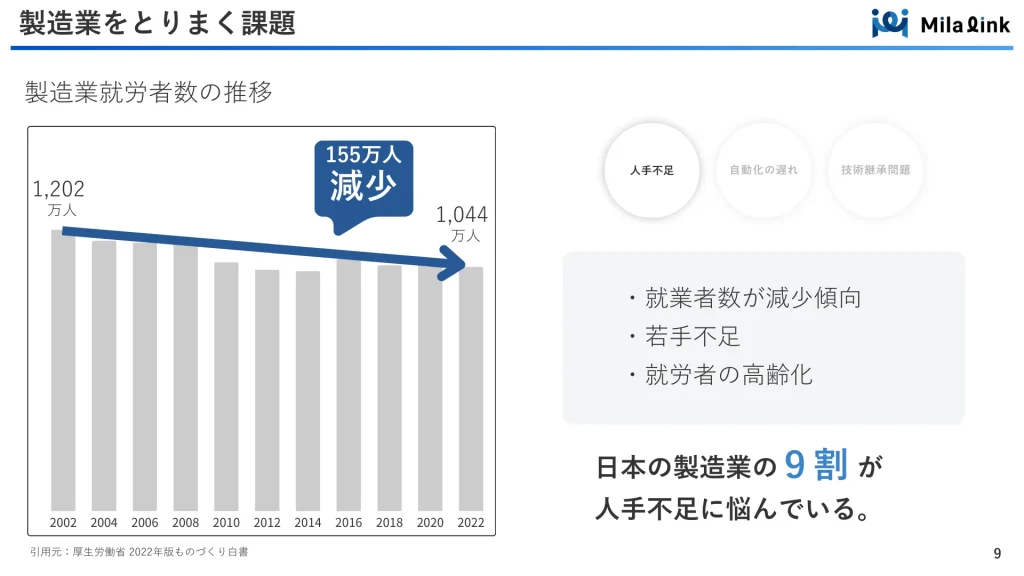
まず、人手不足について。高齢化が加速する日本では、製造業にとどまらず全ての産業で人手不足が叫ばれていますが、製造業においては特にその傾向が顕著に表れています。
スライドのデータは経済産業省が発行している「ものづくり白書」のデータになりますが、今後も少子高齢化による労働人口の減少が続くとみられているため、人手不足の抜本的な解決を図るためには、雇用だけでなく多角的な観点からのアプローチが求められると考えています。
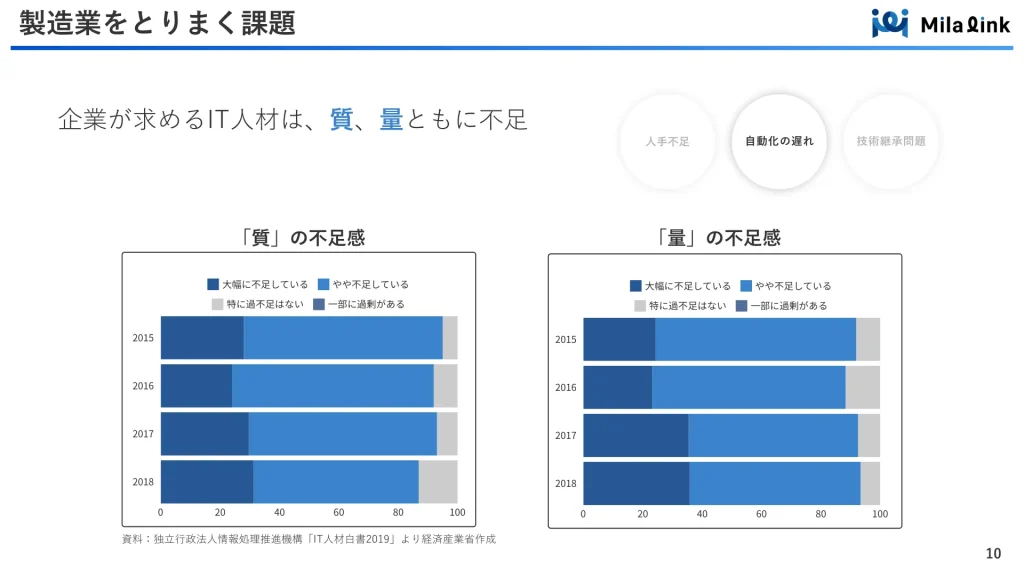
次に、自動化の遅れについて。
製造業では設計関連資料など取り扱うデータが非常に多岐にわたります。
システムやAIによる業務の自動化が課題解決に貢献することが期待される一方で、IT人材の確保の難しさが課題になっています。スライドのグラフは左がIT人材の質に関する不足感を表しており、右は量の不足感を表しているデータです。いずれも「大幅に不足している」と「やや不足している」を合わせた回答(青色で表示)が大半を占めており、課題感の意識はあるものの、雇用の難しさやIT人材の教育の難しさから、不足感はこの4年間でもほとんど改善されていません。
IT人材が足りていない状況で、いかにして自社に合う方法で自動化を進めるかが鍵になってくると考えています。
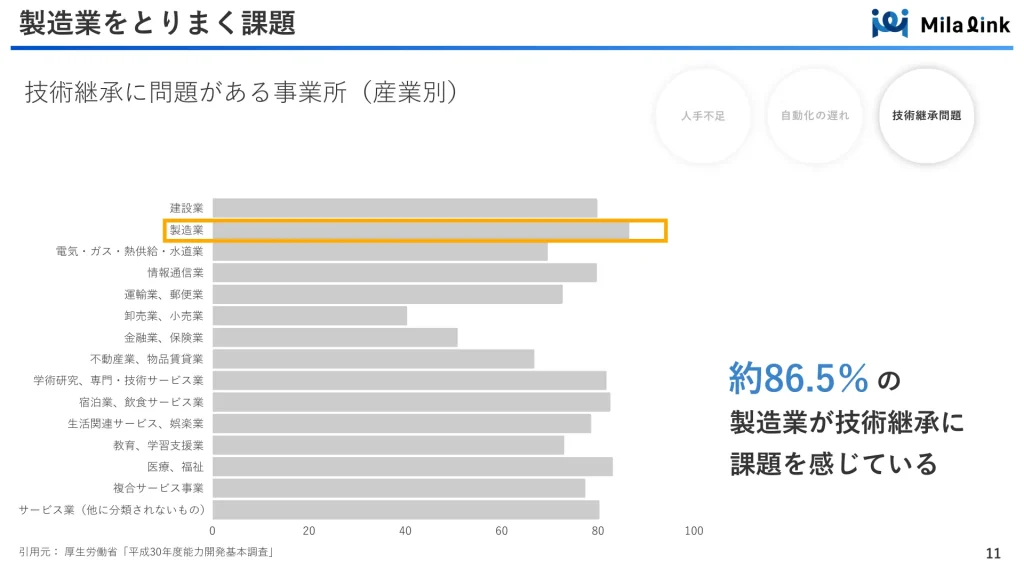
次に、技術継承問題について。
データは産業別の技術継承に問題がある事業所のデータです。この中でも特に製造業は多くの問題があると回答しているのが見られると思います。技術、独自の知見やノウハウを共有・継承していくことは、事業継続の観点から多くの企業で重視されています。もちろん製造業も例外ではなく、技術継承に問題を抱えているケースが非常に多いというところがこのデータでも現れています。
なかなか技術継承が行われない要因としては、先ほどにもあった少子高齢化の問題によって若手人材が不足しているというところがあります。技術継承にそもそも後継者がいないという実情があります。
また、人手不足から人材育成に時間や人員を割けず、せっかく採用した若手人材が育たないうちに退職してしまうといったケースも多くあります。技術継承が適切に行われなければ、生産効率の低下や新製品の開発が難しくなるなどの問題が生じる可能性があります。
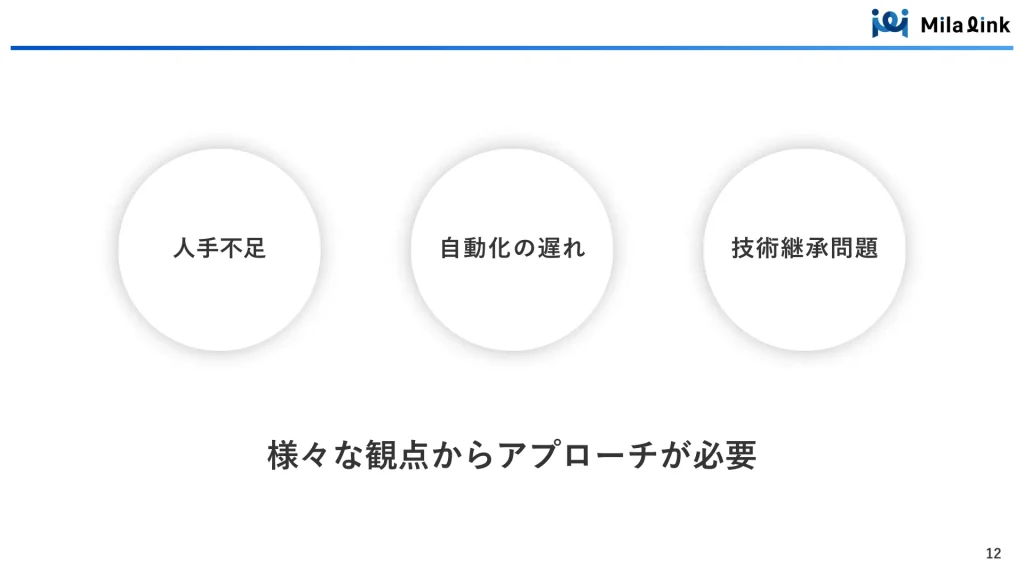
以上のことから、人手不足を解消し、効率化や生産性を最大限に高めることが必要不可欠になってきており、製造業におけるDX推進の重要性はより一層高まりを見せています。
ミラリンクとしましても、この課題を重く受け止めており、これまで人の手で行ってきた業務を自動化することで、既存の作業にかかる時間を削り、業務効率化を目指していく必要性があると考えています。
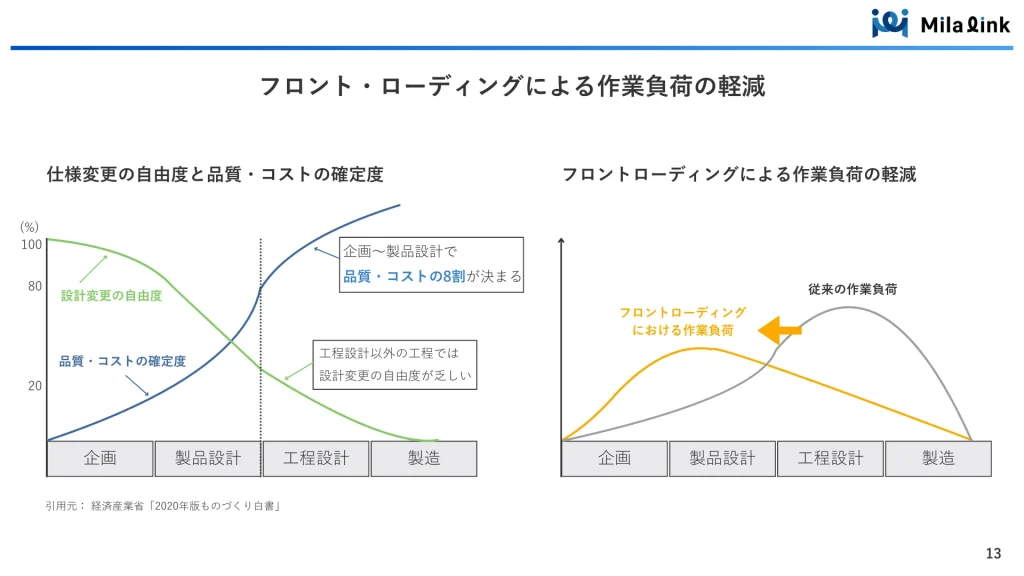
左の図は、商品開発における仕様変更の自由度と品質・コストの確定度を示したものです。開発が進むにつれて製造設備などが確定していくため、仕様変更の自由度はだんだんと低下していき、設計が完了した後の仕様変更の余地はかなり限られたものになってきます。
こういったことから、仕様変更の自由度が高い設計の段階で製品の品質とコストの8割程度が決まると言われています。できるだけ開発の初期段階で設計の業務を効率化させることで、問題点の早期発見や品質向上、後工程での手戻りによる無駄をなくすことが重要になると考えています。
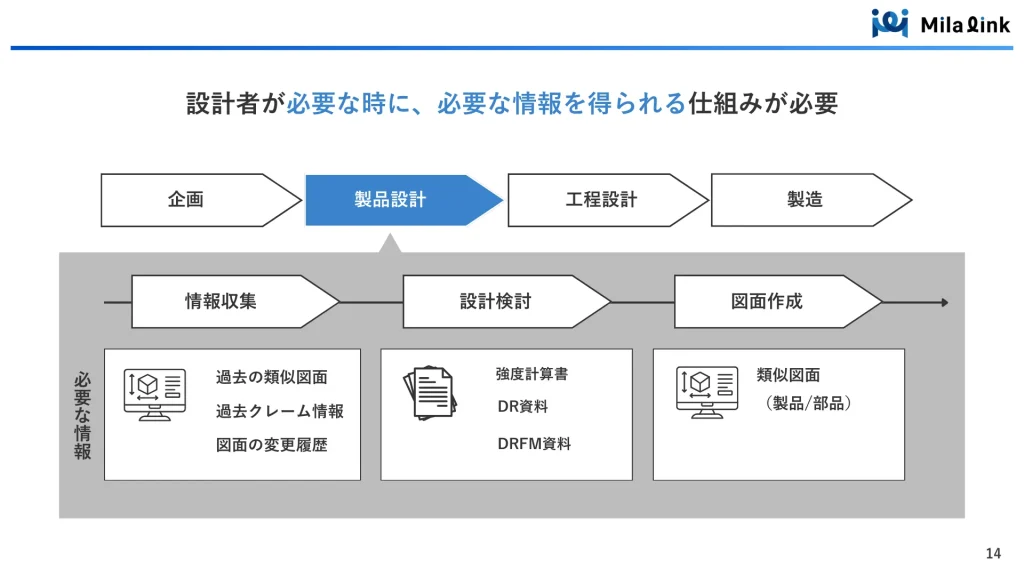
図は、設計者の業務フローの一部を表したものです。
- 情報収集:流用できる図面がないか製品開発の時にシステムで検索をしたり、当時図面を作った担当者に内容を確認するなどの情報収集の業務があります。
- 設計検討:強度計算書やデザインレビューの資料、DRBFM(Design Review Based on Failure Mode)の資料などを検索する場合があります。
- 図面作成:類似する図面の製品図面や部品図面を見ながら行うことがあります。
それぞれのフローで欲しい情報がすぐに検索できればいいのですが、それぞれ保管されているシステムが違うために探すのに時間がかかってしまったり、データが似ているけど1つ1つファイルを開いて欲しい情報があるか中身を確認していく必要があったりと、この検索業務が負担になっているというお話を設計者の方からお聞きすることがよくあります。
データを探す時間が無駄になるだけではなく、「あの人しか知らない」といった属人化のリスクも高まります。こうした「うまく見つからない」状況を放置してしまうと、同じミスを繰り返すだけではなく、貴重なノウハウや知見が時間の経過や人材の移動、退職により失われてしまいます。
設計者が必要な情報を必要なタイミングで素早く正確に検索・共有し、効率的に活用できる仕組みづくりが不可欠であると考えております。
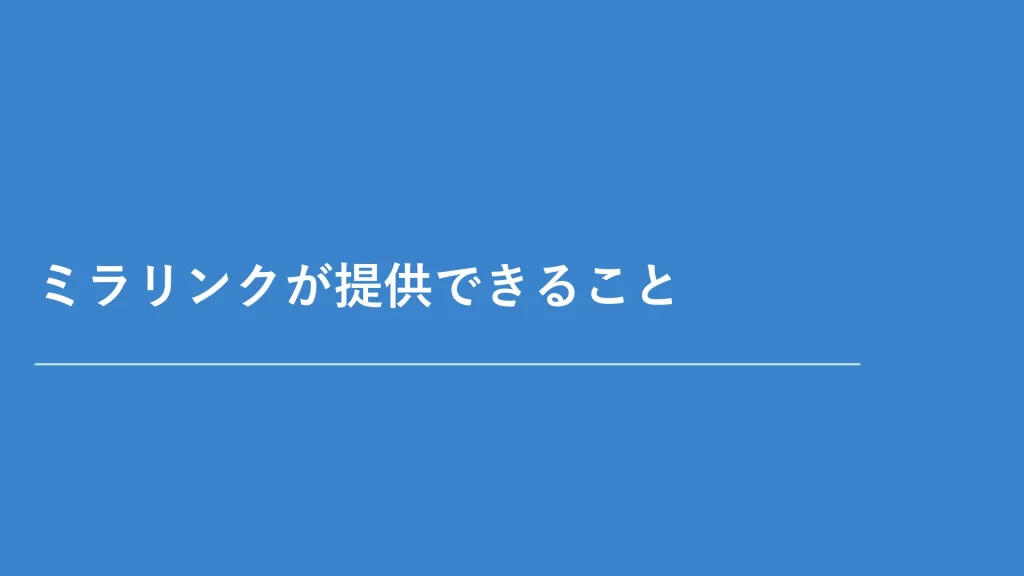
このような課題を我々は、システムによって解決したいと考えております。
ここからは具体的にどように解決できるのか、機能や活用方法をご紹介いたします。
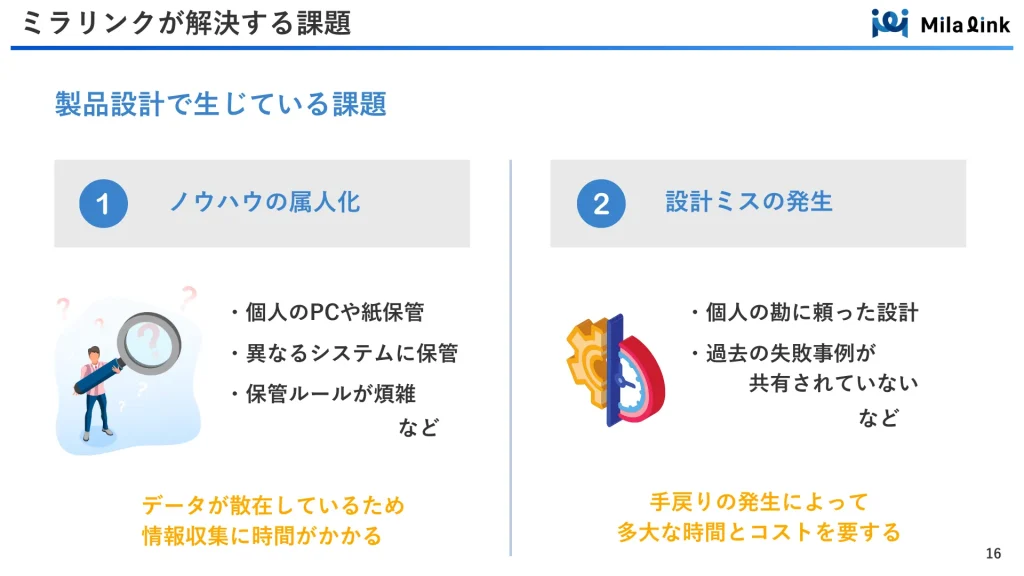
ミラリンクが解決したい課題は、設計部門にフォーカスを当てた「ノウハウの属人化」と「設計ミスの発生」についてです。
まず、ノウハウの属人化について説明します。例えば、製品図面の変更履歴や仕様書などが個人のパソコンのデスクトップに保存されていたり、紙で保管されている場合があります。他にも、それぞれ異なるシステムに保管されていたり、ファイルサーバーへの保管ルールがバラバラで、データ化されているにもかかわらず、結局うまく探すことができず、担当者に聞かないとわからないという状況にあるというお話もよく聞きます。
次に設計ミスの発生について。従業員個人に頼った設計により資料の確認不足のミスが発生したり、過去の失敗事例が共有されていないことによるミスの発生などが考えられます。これらの課題をシステムで解決することを考えております。
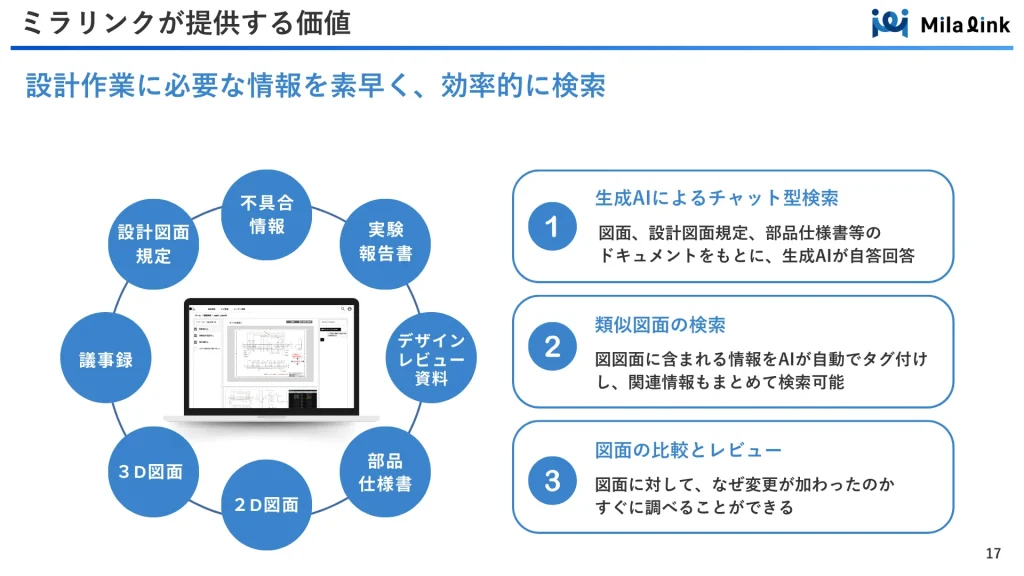
社内に散在する様々な情報をAIに学習させ、必要な時に要約して情報を得ることができるシステムを開発しています。このシステムにより、図面や不具合情報、議事録、仕様書など様々な設計に関わる情報を素早く効率的に検索できます。
主な特徴として、生成AIによるチャット型検索、類似図面の検索、図面の比較レビューといった機能がございます。
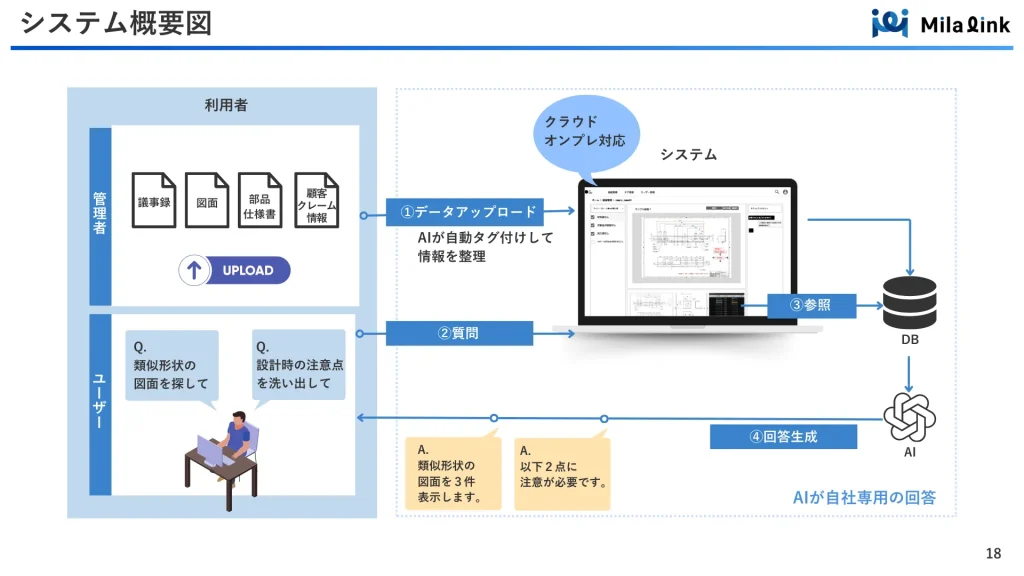
システムの概要図をご覧ください。このシステムはクラウドとオンプレミス、どちらにも対応しており、お客様のご要望に合わせた形でのご提供が可能となっております。
利用者が設計に関わるドキュメントをシステムにアップロードするだけの簡単な操作で、AIに学習させる情報を取り込むことができます。この際にAIがドキュメントの内容を読み取り、情報を自動タグ付けし整理をします。
ユーザーがチャット形式で質問をすると、ドキュメントの内容から関連する情報を回答します。
例えば、「設計時の注意点を洗い出して」と設計者の方が入力すると、過去の失敗事例や使用書を瞬時に参照して「以下の2点に注意が必要です」というようにAIが回答してくれるイメージです。
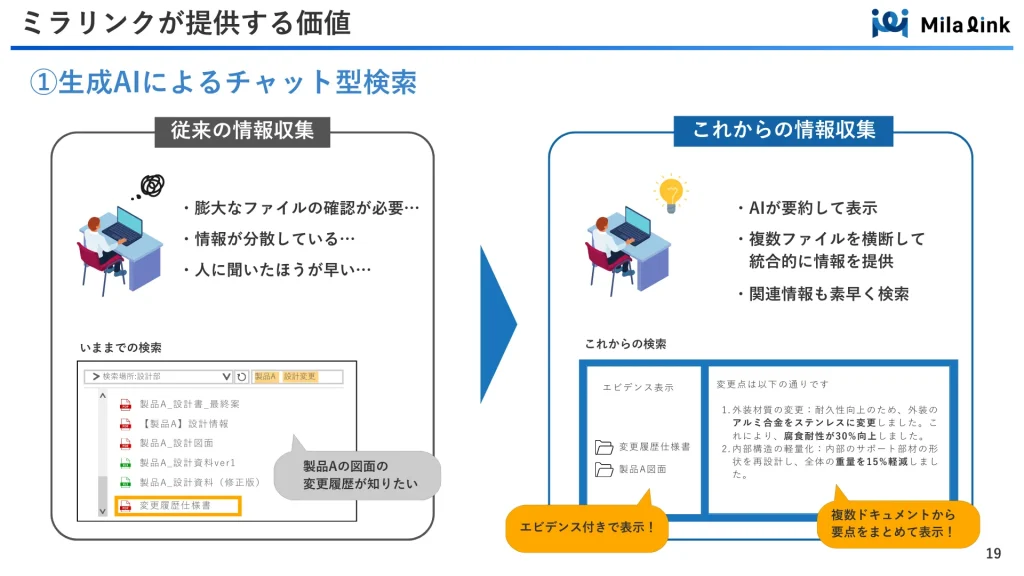
チャット型検索についてご説明します。社内の膨大なデータを学習して自社専用の知識ベースから質問に関する情報をピックアップし、自然なテキストとして返答します。ファイルサーバーでのデータ検索と比較すると、こちらの図で表しているような形になります。
ファイルサーバーのデータ検索では、例えば製品Aの図面の変更履歴が知りたい場合、製品Aという製品名や設計変更というキーワードを入力して検索をかけることがあると思います。そうするとキーワードで引っかかったデータが一覧で表示されるので、知りたい情報が含まれていると思われるデータを一つ一つ開いて確認していく作業が必要です。
これは量が膨大だと確認が大変ですし、別のシステムに保管されていてここでは探せない場合もあります。
一方、AIによるチャット型検索では、右の図のようなイメージになります。
例えば、チャットで「製品A図面の変更履歴を教えて」と入力すると、複数ファイルに含まれた情報をAIがまとめ、要点を整理した状態で回答してくれます。ポイントとしては、要約して表示してくれること、複数ファイルを横断して統合的に情報を提供してくれること、関連情報も素早く検索できることが挙げられます。
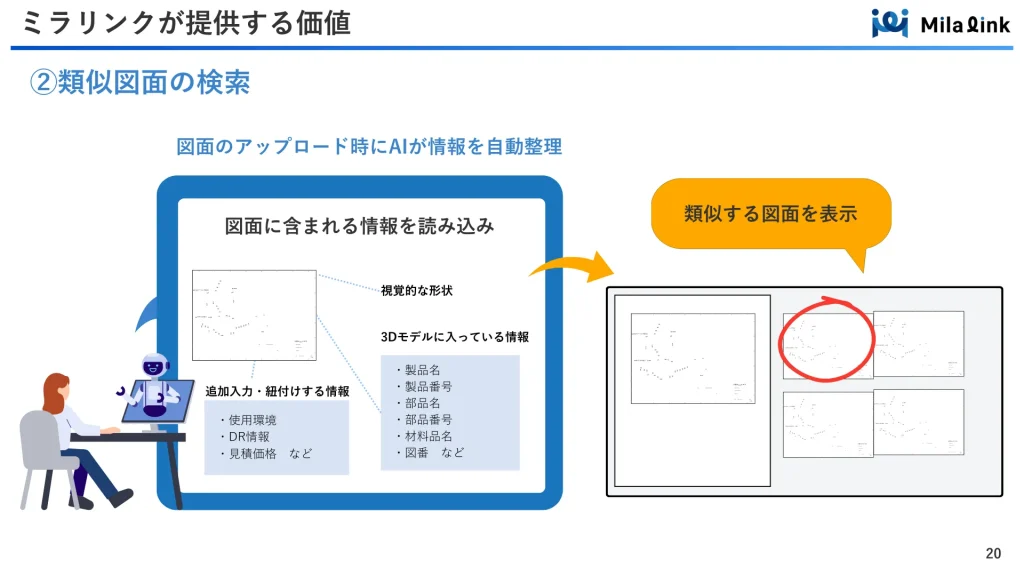
次に、類似図面検索機能についてご紹介いたします。
流用設計を行う場合、設計者は類似した図面を検索する業務があると思います。
そのような場合に、図面を読み込み、類似した図面をピックアップすることができます。システムに図面をアップロードすると、AIが図面に含まれる情報を読み込みます。例えば、図面の視覚的な形状や2D・3Dモデルに含まれているデータが持っている裏の情報(製品名、製品番号、個人名など)を読み込んで、内部で自動的にタグ付けをして情報整理を行います。そうすることで、これらの情報をもとに検索することが可能になります。
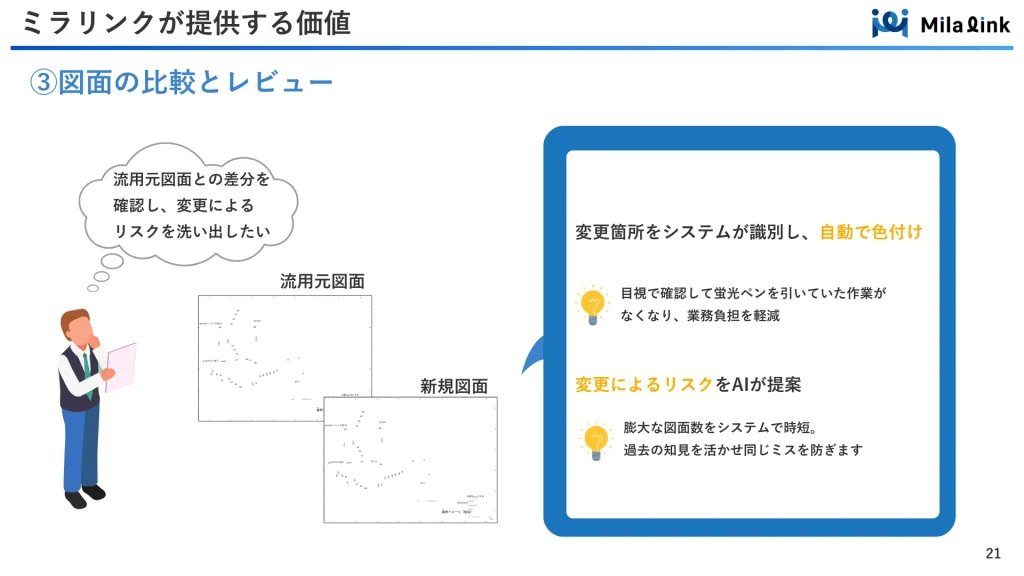
次に、図面の比較とレビュー機能についてです。
流用設計の場合、流用元の図面と今回新しく作った図面の差分を確認し、変更によるリスクを洗い出したいといった確認作業があると思います。
流用元の図面と今回作成した図面を取り込めば、変更箇所をシステムが識別し、自動で差分を色付けして表示してくれます。これにより、従来目視で変更箇所を確認し蛍光ペンで印をつけていたような作業が軽減され、設計者の業務負担を減らすことができます。
さらに、この変更の差分を確認するだけでなく、変更によるリスクをAIが提案してくれる機能もございます。
これは、差分をチェックした上で、どのような理由で変更したのかをテキストでシステムに入力することで、既に取り込んである過去のトラブルやノウハウ情報をもとにAIが注意点を回答してくれます。
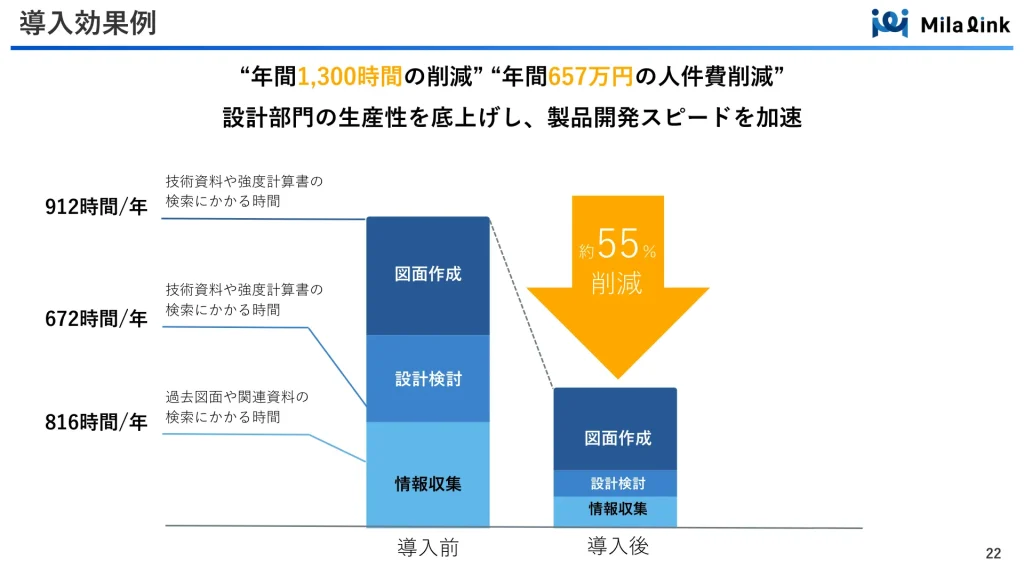
こちらはご参考までに、導入効果の例になります。
設計部門における検索業務は日々少しずつのことですが、年間で見るとかなりの時間を要している場合もあります。
弊社の調査では、実際の設計者が検索にかけている時間を年間で約55%削減できるとのデータがございます。
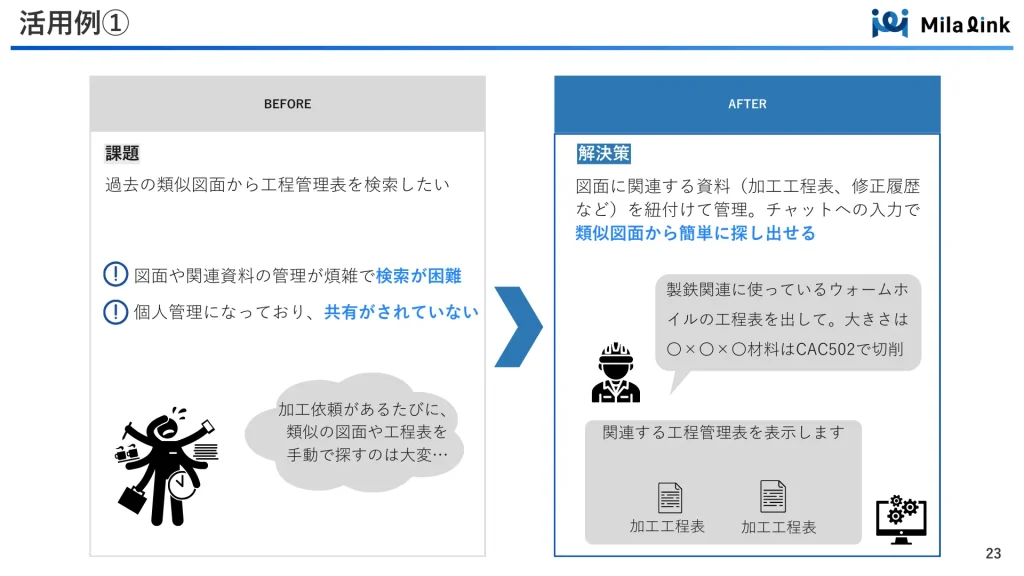
次に、設計者の方の具体的な活用例をご紹介します。
まず1つ目は、図面に付随する資料を探す例です。
新商品開発では、過去の類似製品の設計情報を参考に、新たな製品開発の効率化を図ることが一般的です。この際、従来の図面だけでなく、製造工程に関する情報も参照することで、より詳細な検討が可能になります。しかし、従来の検索方法では、図面や関連資料の管理が煩雑で、必要な情報にたどり着くまでに時間がかかっていました。
本システムでは、AIによる自動タグ付け機能により、図面と関連資料を効率的に管理できます。これにより、チャット形式で簡単な検索を行うだけで、目的とする図面や工程管理表を迅速に探し出すことが可能になります。
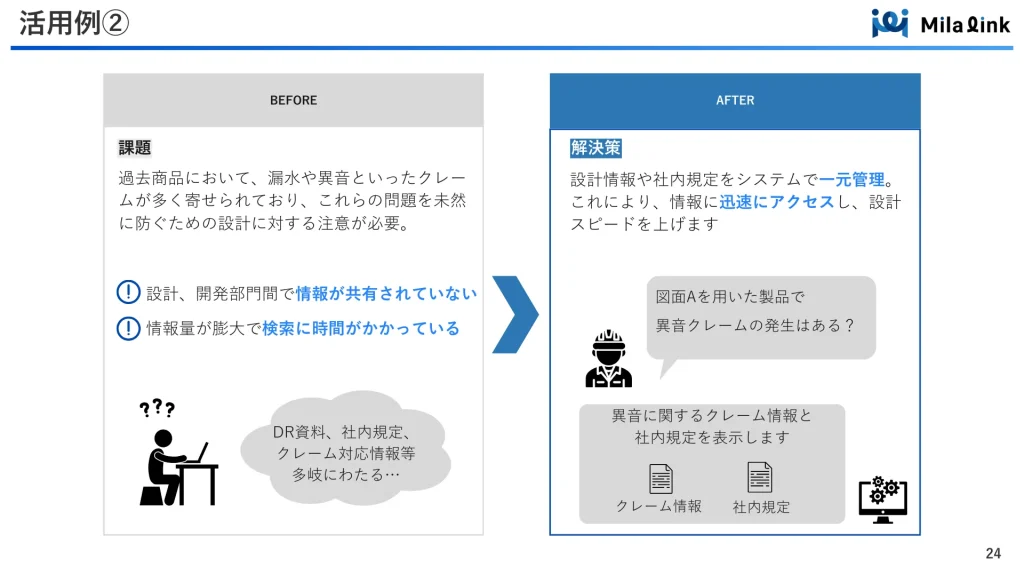
2つ目の活用例は、設計時の注意点を表示する機能です。
過去の製品において、漏水や異音といったクレームが発生した場合、その原因を究明し、同様のトラブルを繰り返さないための設計改善が求められます。
しかし、設計情報が部門間で共有されていないため、過去のクレーム情報にアクセスし、設計に活かすことが困難という課題があります。膨大な情報の中から必要な情報を検索するにも時間がかかり、重要な情報を見落としてしまうリスクがあります。
本システムでは、設計情報や社内規定を一元管理し、AIによる検索機能を強化することで、これらの課題を解決します。例えば、「図面Aを用いた製品で異音クレームが発生した事例はある?」と質問し、関連する図面をアップロードするだけで、過去のクレーム情報や関連する社内規定を迅速に検索できます。これにより、設計者は、過去の情報を活かし、より高品質な製品を開発に役立てることが可能になります。
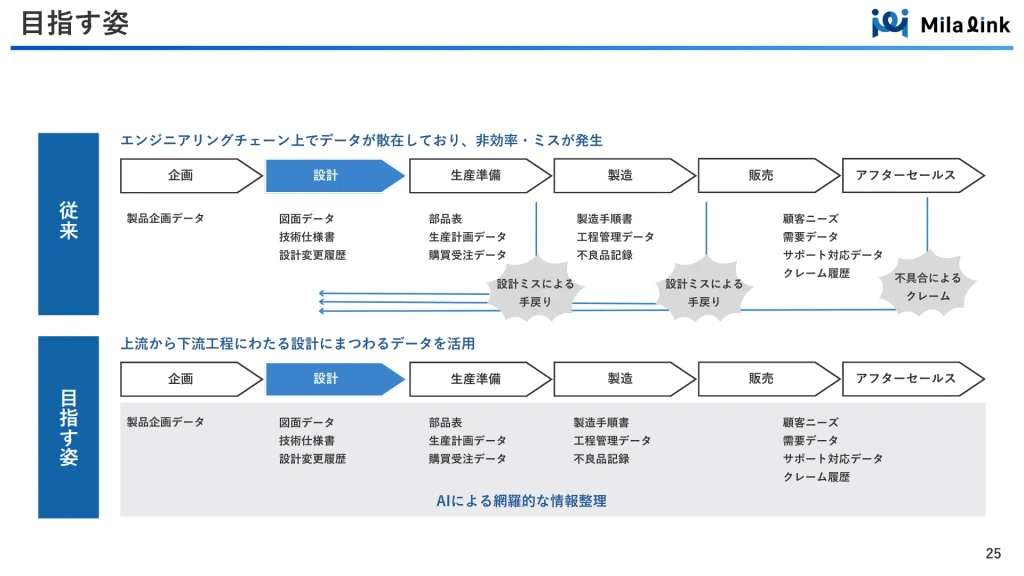
最後に、このシステムが目指す姿についてお話しします。
まずは設計開発部門内に散在するデータの活用からスタートし、最終的には企画から販売、アフターセールスまでのエンジニアリングチェーンと呼ばれる工程全体でのデータ活用を目指します。
これまで部門ごとに管理され、横断的な利用が難しかった設計図面、製造情報、顧客データなどを統合し、AIを活用して網羅的な情報整理を行います。これにより、設計ミスや不具合によるクレームを未然に防ぎ、製品品質の向上と開発効率の改善に貢献します。
以上で私からの説明を終わり、ここからは設計者向けのナレッジ活用例について、技術担当営業の田中からご説明いたします。田中さん、よろしくお願いします。
FMEA(故障モード影響解析)と設計者向けのナレッジ活用例について、より実務に即した形でお話しさせていただきます。今回のセミナーは設計者の方々向けということで、実際に図面を描いたり様々な設計手法を用いてレビューされている方が多いと思います。そこで、FMEAとDRBFMという設計時によく用いられる代表的な開発手法を例に、ナレッジの活用についてお話しいたします。
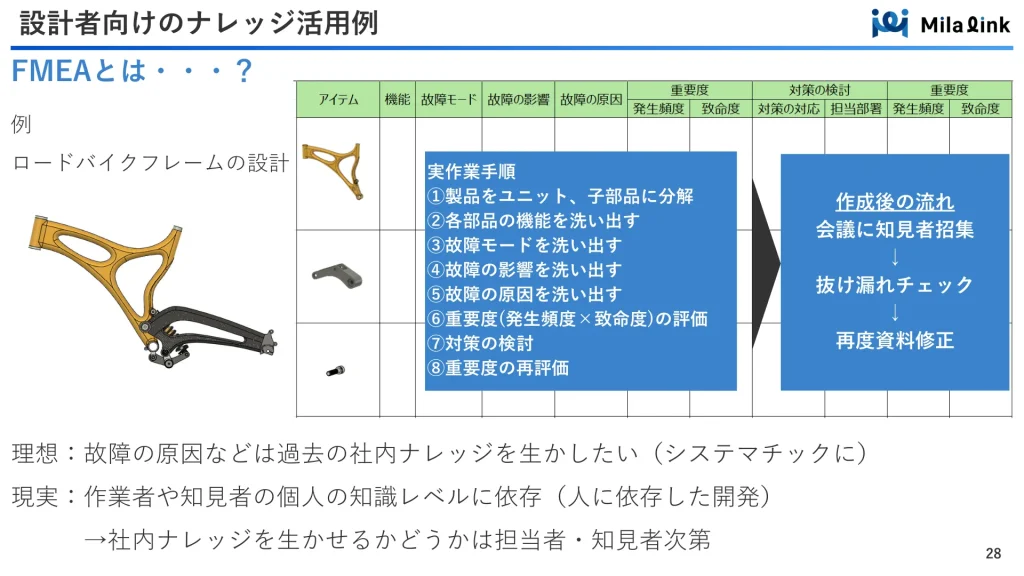
まず、FMEAについてですが、これは製品やプロセスに潜在する故障や問題を予測し、その影響を分析して対策を考えるための手法です。一方、DRBFMは設計変更による潜在的な問題を事前に検討する手法で、主に設計の変更点に着目し、その影響やリスクを深く議論して問題を未然に防ぐことを目的としています。
これらの手法は製造業で広く用いられていますが、多くの企業が共通して抱える課題があります。
それは、資料作成において社内のノウハウと連携ができていないこと、アウトプットが作成者個人のスキルや会議参加者、資料チェック担当者の経験に依存してしまうこと、そして作成の負荷が大きく、作成自体が目的となってしまい、本来の目的であるレビューにまで至らないことです。
FMEAの具体的な作業プロセスを、ロードバイクのフレーム設計を例に説明します。
まず、製品を部品レベルまで分解し、各部品の機能を洗い出します。次に、各機能が失われる状態(故障モード)を特定し、その故障が上位製品に与える影響を分析します。例えば、フレームが破損した場合、乗車中の人が怪我をする可能性があるといった具合です。
これらの評価が終わったら、故障の発生確率や深刻度を考慮して重要度を評価し、重要度の高い順に対策を検討します。最後に、対策を踏まえた再評価を行います。
理想的には、故障の原因などは過去の社内ノウハウや不具合データ、環境要因などを統合したシステムから自動的に反映されるべきです。しかし現実には、作業者や審査者の個人的な知識レベルに依存してしまっており、ノウハウの活用が担当者次第になっているのが実情です。
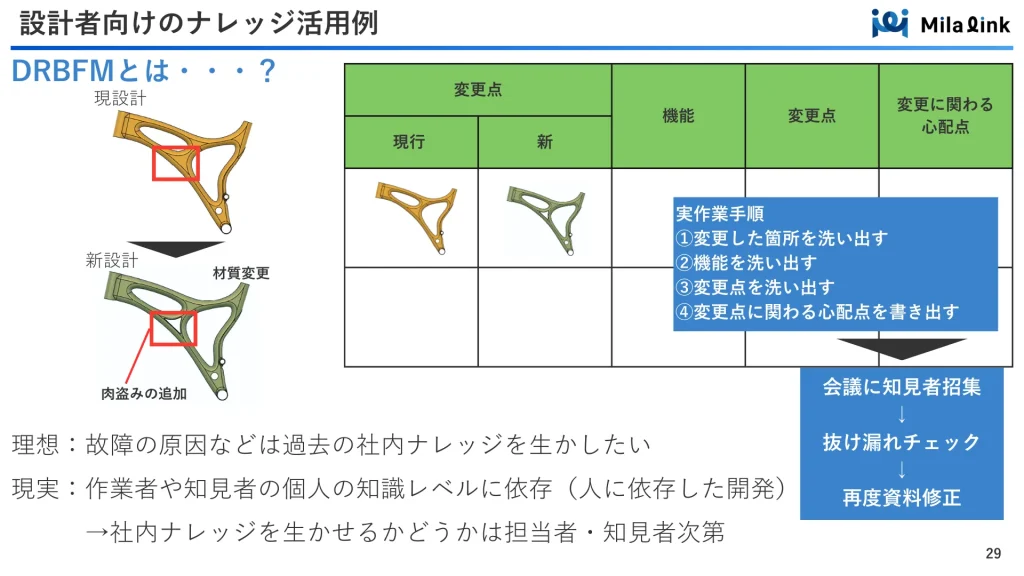
DRBFMについても同様の課題があります。DRBFMとは設計変更時のリスク分析手法です。例えば、フレーム設計においてコストダウンのための材質変更や軽量化のためのリブ追加を行う場合、以下のステップを踏みます。
- 変更箇所の洗い出し
- 変更部品の機能確認
- 変更理由の明確化(例:材質変更、リブ追加)
- 変更に伴う新たなリスクの特定
これらのステップを経て、関係者が集まって変更内容をチェックし、必要に応じて仕様を修正します。しかし、多くの企業では過去の経験や社内ノウハウを十分に活用できていないのが現状です。
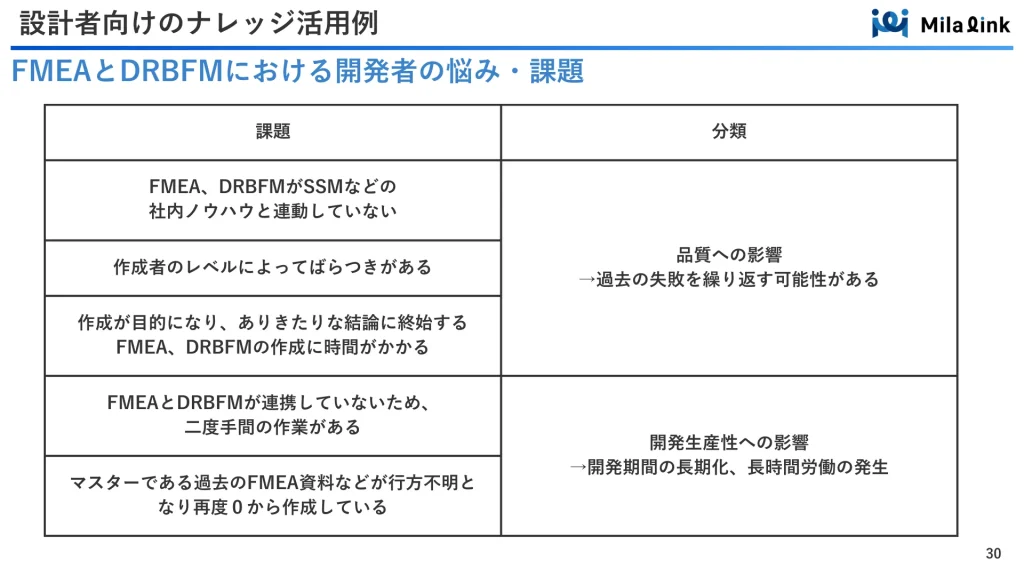
FMEAやDRBFMに関する課題をまとめると
- 社内ノウハウシステムとの連携不足
- 作成者のスキルレベルによる品質のばらつき
- 資料作成自体が目的化し、本来の設計レビューに時間を割けない
- 部門間や担当者間でのナレッジ共有の不足
- 過去の類似製品の資料が有効活用されず、類似作業の繰り返し
- マスターデータや過去のFMEA資料の紛失による再作成
これらの課題は、品質面では過去の失敗を繰り返すリスクを高め、開発生産性の面では開発期間の長期化や長時間労働の原因となっています。
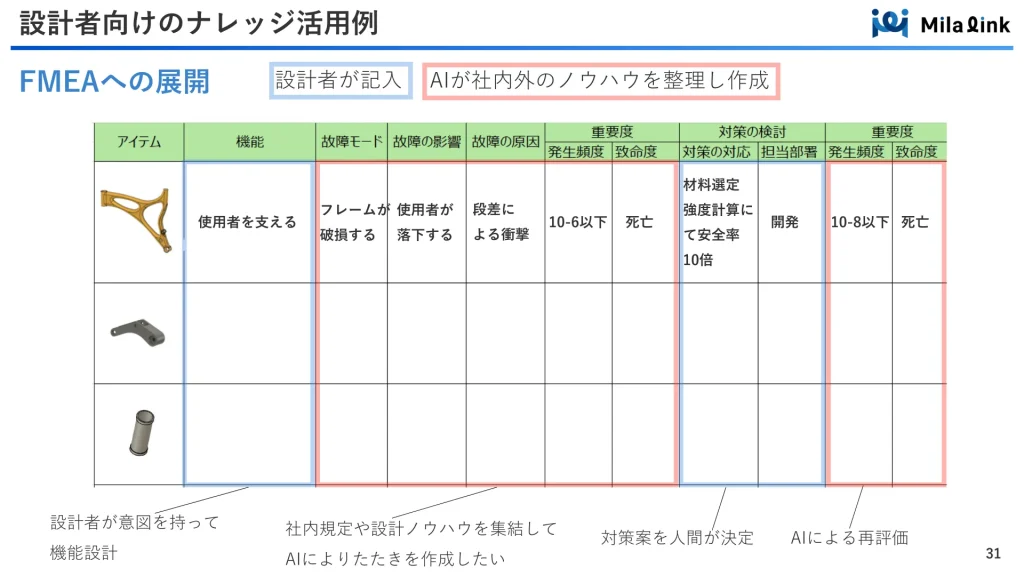
そこで、FMEAのナレッジ展開において、設計者の責任で記入すべき部分とAIやシステムが自動で作成できる部分を区別することが重要です。
例えば
- 設計者が記入:部品の機能(設計意図を反映)
- AIが自動生成:故障モード、故障の影響、故障の原因、重要度(社内ノウハウを活用)
- 設計者が対応:高リスク項目への対策立案
- AIが支援:対策後の再評価
このように、設計者の意思決定と社内規定・ノウハウを組み合わせることで、効率的にFMEAを作成できます。
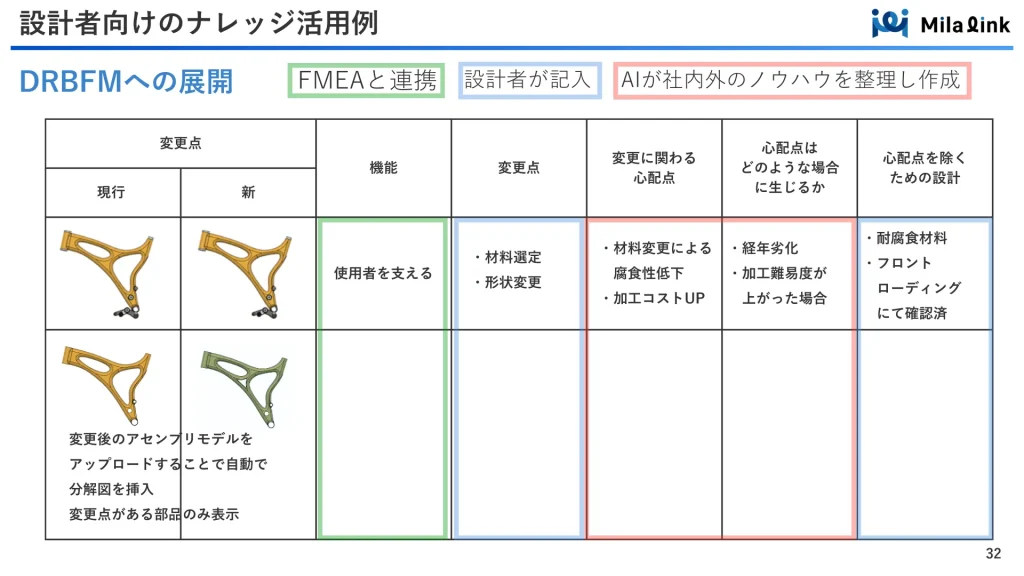
DRBFMについても同様のアプローチが可能です。
- 現行および変更後の3Dモデルを準備
- AIが自動で機能や変更箇所を特定
- 設計者が変更理由を入力
- AIが社内外のノウハウを基に潜在的リスクを提示(例:材料変更による耐食性低下、コスト上昇、経年劣化、加工難易度上昇)
- 設計者が最終的な失敗防止策を決定
現在、弊社では変更後のアセンブリモデルをアップロードすると、AIが自動的に分解して必要な情報を抽出し、画像を含めたレポートを生成する機能を開発中です。
それでは、ここからはエンジニアの近藤より、デモンストレーションをいたします。
このFMEA/DRBFM AI自動化システムのデモをご紹介します。使い方は簡単で、STEPファイルをアップロードするだけです。AIが自動的にモデル全体とその構成部品を分解して表示します。
例えば、複数の部品で構成されるアセンブリの全体と各部品(部品A、部品Bなど)を表示し、STEPファイルから全ての名称も取得します。
実際のファイルは約15の部品で構成されています。各部品の名称、機能、故障モード、故障の影響を評価します。
例えば、機能欄に人間が一部入力すると(例:自転車のフレームの一部が「荷重を支える」「前輪固定ユニットと接続」「ギアを固定」など)、AIが社内ノウハウを参照しながら故障モードと故障の影響を予測します。
これにより、FMEAの効率的な作成が可能になります。AIが叩き台を作成し、人間がチェックすることで、作業の手間を大幅に削減しつつ、品質のばらつきも抑えられます。
出力結果は社内の開発規約やマニュアル、JIS規格なども参照しながら生成できます。
また、インターフェースは各顧客ごとにカスタマイズ可能で、例えばExcelファイルに画像を埋め込んだ形式でのアウトプットも可能です。AIのサポート付きで入力し、最後に画像付きでエクスポートして社内文書として使用できます。
エクセルの形式や画像の配置などもカスタマイズ可能ですので、ご要望に応じて柔軟に対応いたします。
このように、FMEAやDRBFMのAI自動化により、以下の効果が期待できます。
- 社内ノウハウシステムとの連携による自動的なナレッジ反映
- 個人差の軽減と資料作成時間の大幅削減
- 本来の目的である設計レビューへの注力
- 品質向上への貢献
- テーマごとのFMEA/DRBFM連携による重複作業の撲滅
弊社では、製造業の現場経験豊富なコンサルタントが親身に対応いたします。既存のオンプレミスシステムとの連携やデータのアップロード方法、過去データの取り込み方など、お客様のニーズに合わせて柔軟に対応いたします。ご興味がありましたら、お気軽にご相談ください。
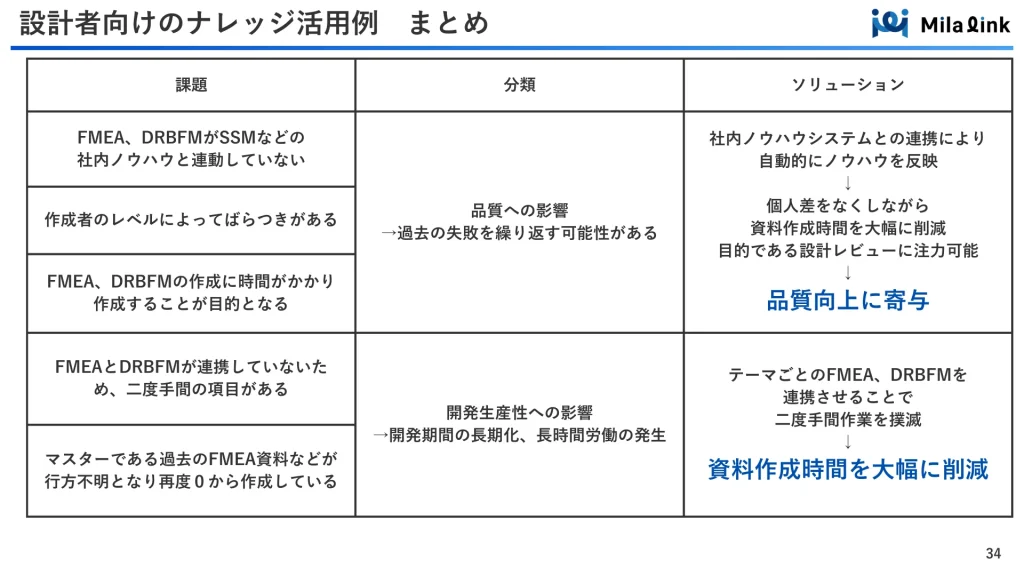
ここまでのまとめです。
FMEAやDRBFMが社内ノウハウと連動していなかったり、作成者のレベルでばらつきがあったりする課題がありました。
これを作ること自体が目的となってしまい、時間がかかってしまうという問題もありました。
また、マスターデータである過去のFMEAなどが行方不明となり、再度ゼロから作成してしまうこともありました。
そういった課題に対して、弊社が提供させていただきたいソリューションは、社内ノウハウシステムとの連携により自動的にノウハウを反映することです。これによって個人差をなくしながら、資料作成時間を大幅に削減し、本来の目的である設計レビューに注力することが可能になります。
結論としては、品質向上に大きく寄与できると考えています。さらに、テーマごとのFMEA/DRBFMを連携させることで重複作業を撲滅でき、資料作成時間を大幅に削減できるという、2つの大きな効果をご提供できるのではないかと考えております。
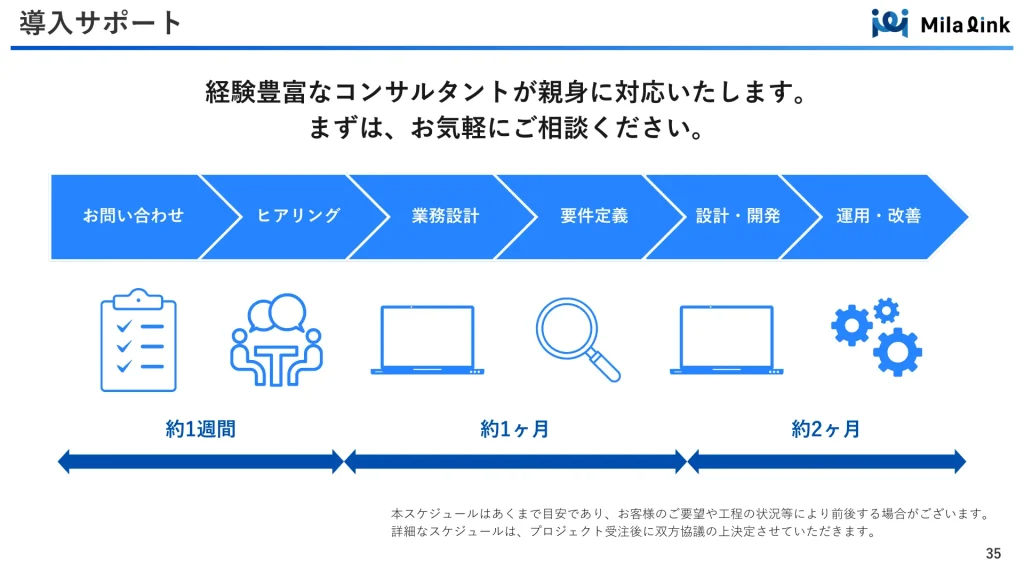
続いて、導入サポートについてご説明いたします。
弊社では、実際の製造業の現場経験のあるコンサルタントが親身に対応いたします。
まずは、既存のオンプレミスシステムとの連携の可能性や、データのアップロード方法、過去データの取り込み方について、お客様の要件をお聞きして決めていきます。
もし業務の中で使えそうな部分があると思われる方や、少しでもご興味をいただけた方がいらっしゃいましたら、まずはお気軽にご相談いただけますと幸いです。本日のセミナーを通してご質問事項やご相談内容などがありましたら、お気軽にお問い合わせいただければ幸いです。
セッションは以上となります。ご清聴いただき、ありがとうございました。
高浪さん、田中さん、近藤さん、皆さんありがとうございました。