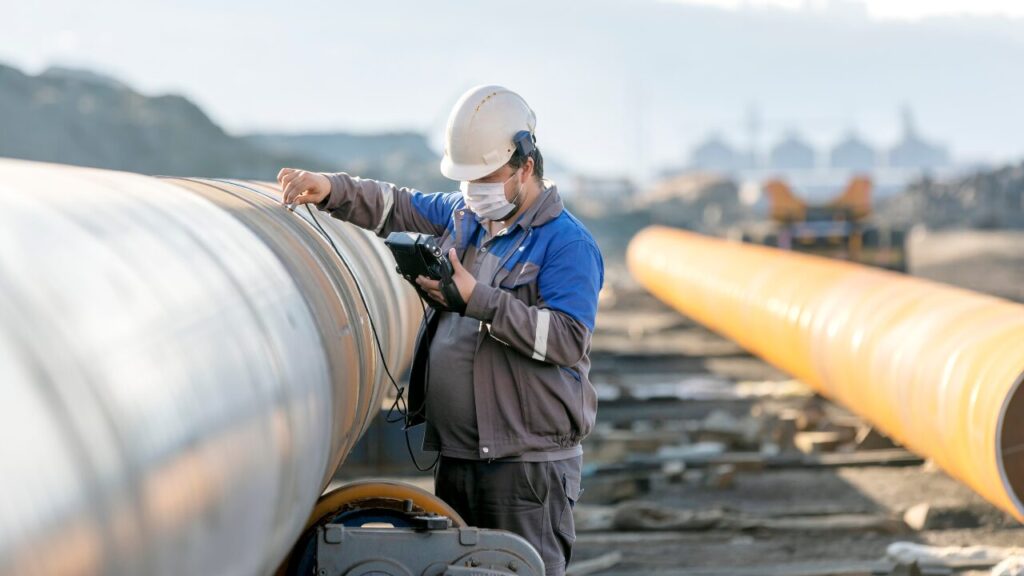
製造業において品質を高めるための手法として「NDI(非破壊検査)」があります。NDIは製品や部品を破壊することなく内部や表面の状態を評価する技術で、航空宇宙、建設、機械など幅広い分野で活用されています。本記事では、NDIの基本的な仕組みと種類、導入することで得られるメリット、さらに製造現場での実践ポイントについて解説します。
NDI(非破壊検査)とは?
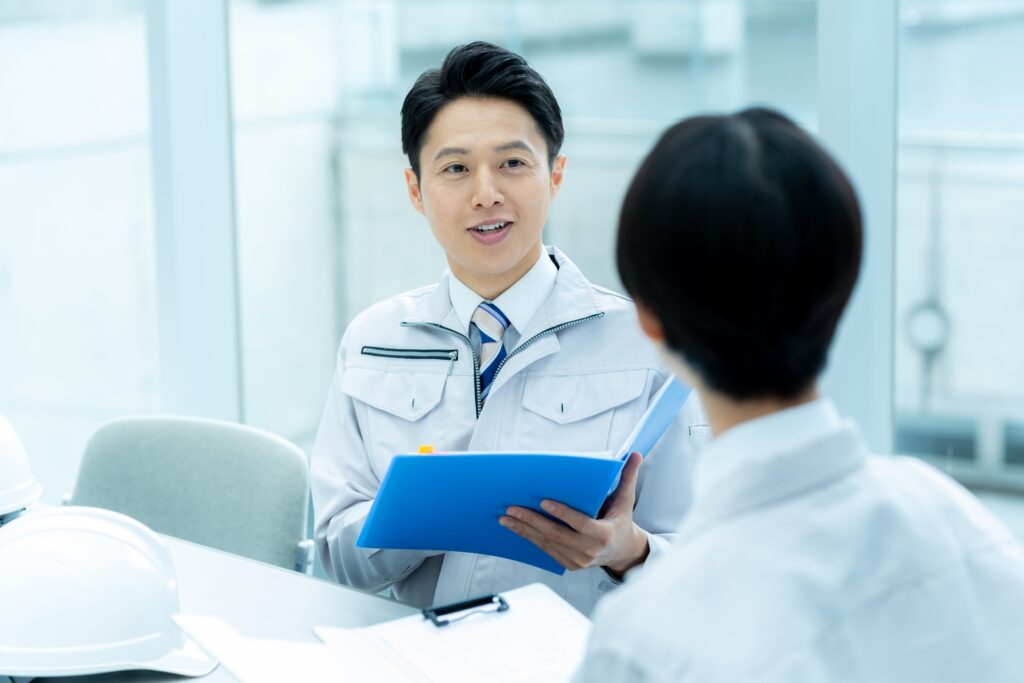
NDI(Non-Destructive Inspection)とは、製品や材料を破壊せずにその品質や構造を検査する方法を指します。従来の破壊検査では、製品の一部を壊して内部の状態を確認する必要がありましたが、NDIではそれを避け、製品の性能や耐久性を確保したまま検査が可能です。
NDIの基本的な特長は以下の通りです。
- 製品を破壊せずに検査が可能:検査後も製品や部品を使用可能。
- 経済的効率の向上:廃棄物が減少し、検査コストの削減につながる。
主なNDIの種類
NDIにはさまざまな方法があり、それぞれの技術が異なる検査ニーズに応じています。代表的な検査方法を以下に紹介します。
1. 超音波検査(UT: Ultrasonic Testing)
超音波を利用して材料内部の欠陥を検出します。音波が異物や空隙に当たると反射する特性を利用し、内部の状態を確認します。
- 用途:内部検査
- 利点:表面に出ていない内部の欠陥を検出可能、欠陥の位置や深さを正確に測定可能、放射線検査と比較して安全
2. 放射線検査(RT: Radiographic Testing)
X線やγ線を照射して、材料内部の欠陥を画像として記録します。レントゲン撮影のようなイメージです。
- 用途:内部検査
- 利点:表面に出ていない内部の欠陥を検出可能、接触媒質が不要
3. 磁粉探傷検査(MT: Magnetic Particle Testing)
磁力を利用して、鉄や鋼など磁性体材料の表面や近くの欠陥を検出します。欠陥部分に磁粉が集まる現象を観察します。
- 用途:磁性体の表面検査
- 利点:表面の微細な亀裂を検出可能、強磁性体に対して高感度で検査可能
4. 浸透探傷検査(PT: Penetrant Testing)
液体を材料表面に浸透させ、欠陥部分に溜まった液体を可視化することで不良を検出します。
- 用途:表面検査
- 利点:表面の微細な亀裂を検出可能、金属以外の材料にも適用可能
5. 渦流探傷検査(ET: Eddy Current Testing)
電磁誘導を利用して、金属材料内部の欠陥や表面の異常を検出します。
- 用途:導電性材料の表面検査
- 利点:表面の微細な亀裂を検出可能、非接触で検査可能
製造現場でのNDI導入メリット
NDIを製造現場に導入することで、以下のような多くのメリットを得ることができます。
1. 製品の品質向上
微細な欠陥や不良を早期に発見できます。これにより、顧客に高品質な製品を提供できるようになります。
2. コスト削減
従来の破壊検査では、検査のたびにサンプルを消費する必要がありましたが、NDIでは製品をそのまま検査可能です。これにより、材料の無駄を削減できます。
3. 生産効率の向上
自動化技術と組み合わせることで、検査作業をさらに短縮できます。
4. 安全性の確保
製品の欠陥を未然に発見できるため、トラブルや事故を防ぐことができます。特に航空機や自動車など、安全性が重要な製品で大きな効果を発揮します。
製造現場でNDIを導入する際のポイント
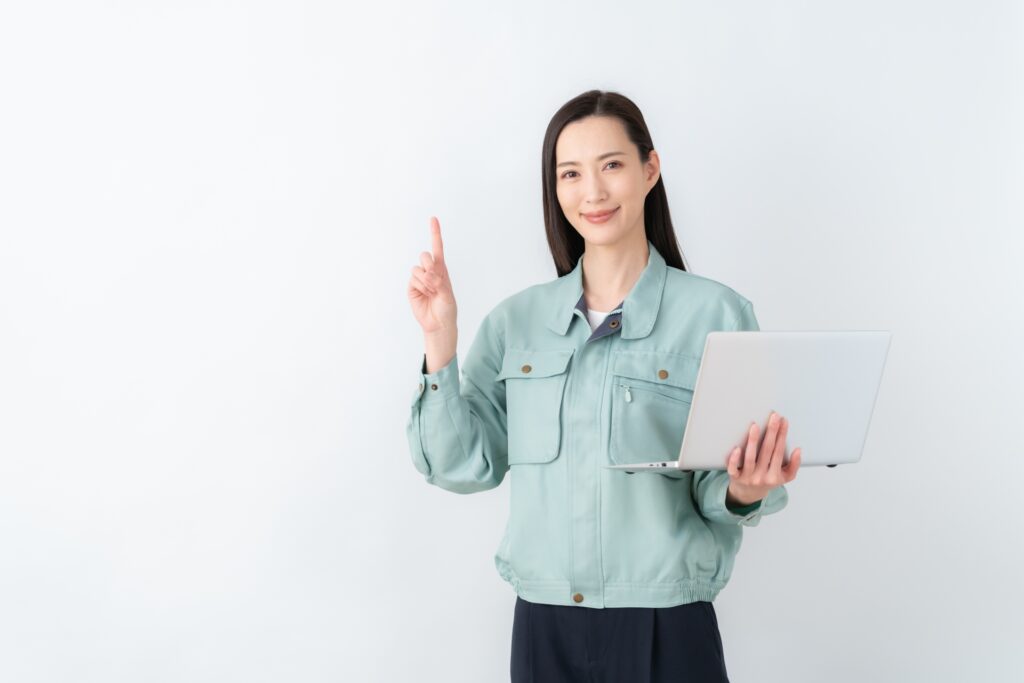
NDIを効果的に導入するためには、以下のポイントを押さえることが重要です。
1. 検査目的に応じた技術選定
製品の素材や形状、検査対象に応じて適切なNDI技術を選ぶ必要があります。例えば、金属部品の内部検査には超音波検査が適しています。
2. 専門知識を持つ人材の確保
NDIは高度な技術を要するため、検査に必要なスキルを持つ人材の確保や育成が欠かせません。
3. 適切な設備投資
初期導入時には検査装置や周辺設備への投資が必要です。ただし、長期的なコスト削減効果を考慮すれば、十分に投資価値があります。
4. 品質管理システムとの連携
検査結果をデータとして蓄積し、品質管理システムと連携させることで、製品品質をさらに向上させることができます。
まとめ
NDI(非破壊検査)は、製品や部品の品質を向上させるための強力な手段です。その高い精度と効率性は、製造現場でのコスト削減や安全性向上にも大きく寄与します。一方で、導入時には技術の選定や人材の育成、設備投資が求められるため、計画的に進めることが重要です。
もし、現在の検査工程で課題を感じているのであれば、NDIの導入を検討してみてはいかがでしょうか?より高品質な製品を提供し、競争力を高めるための一歩として、有益な選択肢となるでしょう。