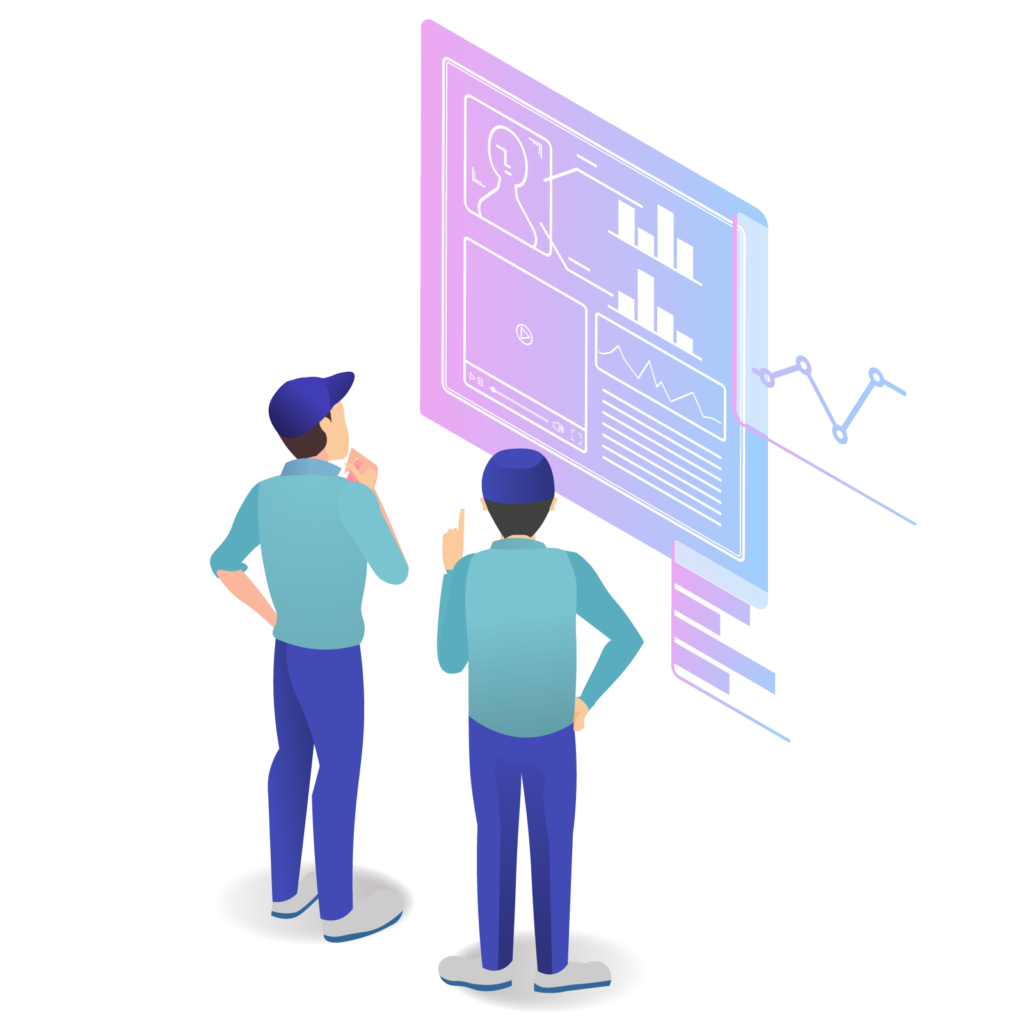
製造業において、品質の安定化や生産効率の向上は常に求められる課題です。その解決策の一つとして「標準化」があります。標準化を導入することで、作業のばらつきを減らし、品質を均一に保つだけでなく、コスト削減や生産性向上にもつながります。
しかし、「標準化を進めたいが、どこから手をつければよいかわからない」「具体的なメリットがイメージしづらい」という方も多いのではないでしょうか。そこで本記事では、製造業における標準化の基本を押さえつつ、導入メリットや実践のポイントを詳しく解説します。
標準化とは?製造業における基本概念
標準化とは、業務や作業手順、製品仕様などを一定のルールに統一することを指します。製造業では、特に以下の3つの観点で標準化が進められます。
- 作業の標準化
- 組立手順や加工方法を統一し、作業員ごとのばらつきをなくす
- 製品の標準化
- 部品や仕様を共通化し、設計の効率化やコスト削減を図る
- 管理の標準化
- 品質管理や生産計画のルールを統一し、業務の最適化を行う
これにより、誰が作業しても一定の品質を保ちやすくなり、ムダの削減やトラブルの未然防止につながります。
製造業における標準化のメリット
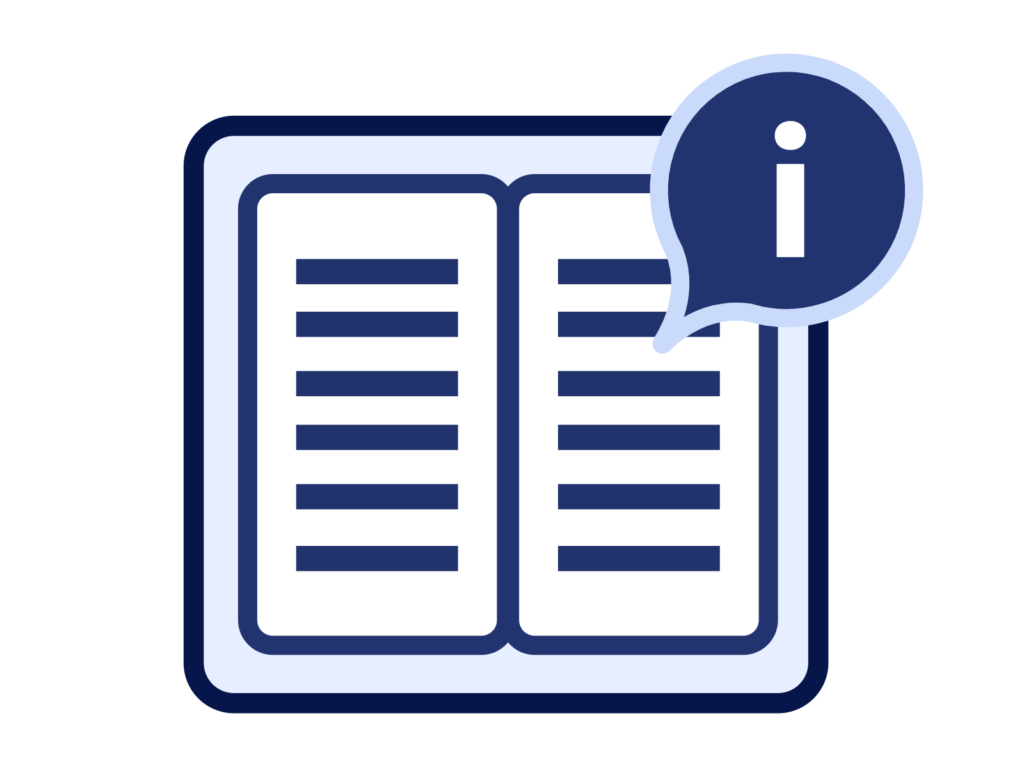
標準化を導入することで、現場の管理や生産活動にどのような効果があるのでしょうか?主なメリットを紹介します。
1. 品質の安定と向上
作業方法や使用する部品を統一することで、製品の品質が均一化され、不良率の低減につながります。また、問題が発生した際の原因特定が容易になり、迅速な対応が可能になります。
2. 生産効率の向上
標準化により、作業が効率化され、無駄な動作や手戻りが削減されます。例えば、作業手順をマニュアル化し、作業員全員が同じ方法で作業を行うことで、生産性が向上します。
3. コスト削減
標準化によって、無駄な工程や材料の使用を削減できるため、コストを抑えることができます。また、部品の共通化を進めることで、調達コストや在庫管理の負担も軽減されます。
4. 教育・技術継承の容易化
作業手順が統一されていると、新入社員や異動してきた社員への教育がスムーズになります。熟練者のノウハウを標準化し、マニュアル化することで、技術の属人化を防ぐことができます。
5. トラブルの予防とリスク低減
標準化によって、業務のルールが明確になるため、ヒューマンエラーの発生を抑えることができます。また、品質管理の基準が統一されることで、クレームやトラブルの発生率を低減できます。
標準化を進めるための具体的な手順
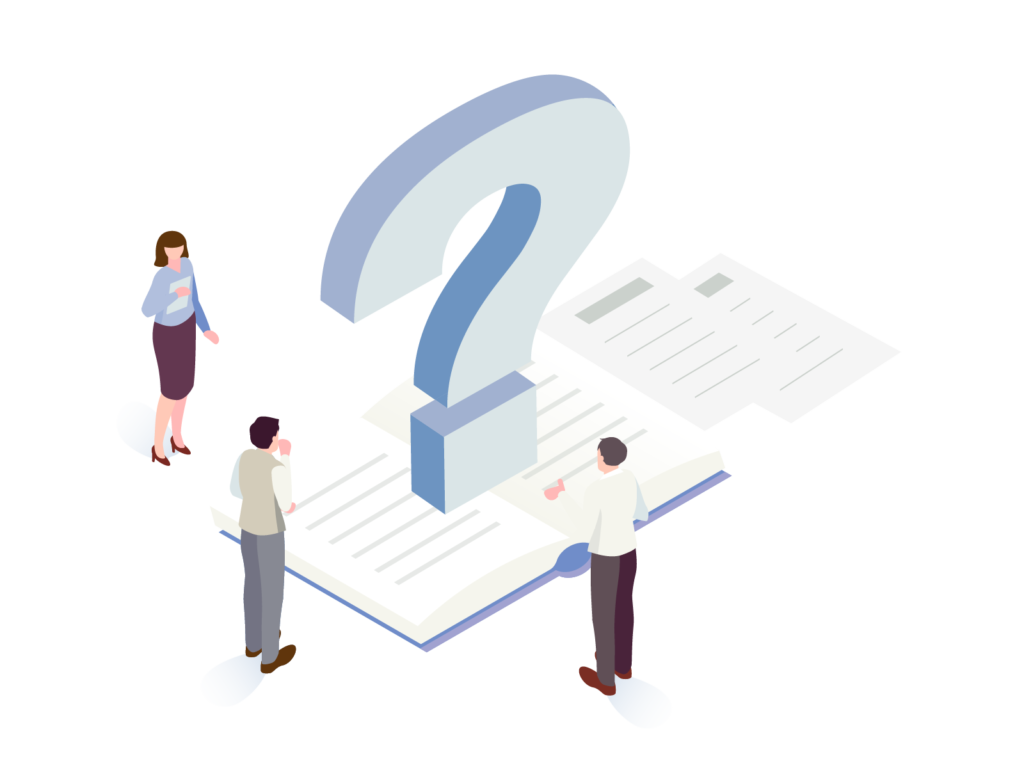
標準化を実施する際には、いくつかのステップを踏むことが重要です。以下の手順で進めると、効果的に導入できます。
1. 現状の課題を把握する
まずは、自社の製造プロセスや作業手順の中で、ばらつきが発生しているポイントを特定します。例えば、「作業員ごとに手順が違う」「品質にばらつきがある」といった問題が標準化の対象となります。
2. 標準化の方針を決める
次に、どの部分を標準化するのかを明確にし、優先順位を決めます。作業手順を標準化するのか、部品の共通化を進めるのか、品質管理のルールを統一するのかなど、目的をはっきりさせることが重要です。
3. 標準化のルールを策定する
標準化する項目が決まったら、具体的なルールを策定します。作業手順の場合は、マニュアルを作成し、誰が見てもわかる形にすることが重要です。また、製品の標準化を進める場合は、使用する部品や設計ルールを明確に定めます。
4. 試験導入とフィードバック
策定した標準化ルールを一部の工程で試験的に導入し、効果を検証します。現場の意見を取り入れながら、必要に応じてルールを修正し、より実用的なものにしていきます。
5. 全体展開と定着化
試験導入で問題がなければ、標準化を全社的に展開します。定期的にルールの見直しを行い、標準化の維持・改善を図ります。継続的なフォローが重要になります。
標準化を成功させるためのポイント
標準化を進める際には、いくつかのポイントを押さえることで、よりスムーズに導入が進みます。
1. 現場の意見を取り入れる
標準化は、現場で実際に作業を行う人が使いやすいものでなければ定着しません。作業者の意見を聞きながら、無理のない形で進めることが重要です。
2. 過度な標準化を避ける
標準化しすぎると、柔軟な対応が難しくなることもあります。特に、カスタム対応が必要な業務では、標準化の範囲を慎重に見極める必要があります。
3. 教育とマニュアルの充実
標準化を導入する際には、教育とマニュアルの整備が欠かせません。作業者が標準化の目的を理解し、正しく実行できるように研修を行うことが重要です。
4. 継続的な改善を行う
標準化は一度決めたら終わりではなく、定期的な見直しが必要です。現場の状況や市場の変化に応じて、標準をアップデートしていくことが求められます。
まとめ
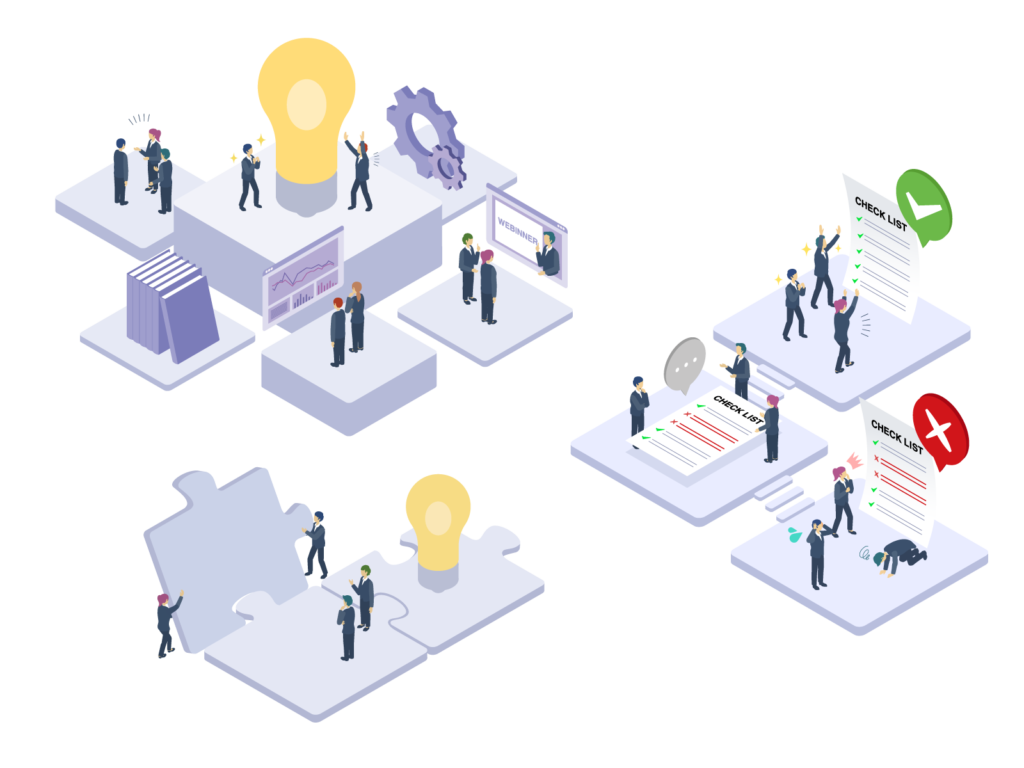
標準化は、製造業における品質向上や生産効率の改善に欠かせない取り組みです。作業のばらつきをなくし、品質を安定させることで、コスト削減やリスク低減にもつながります。
しかし、標準化を進めるには、現場の理解や適切なルール作りが重要です。まずは、現状の課題を把握し、段階的に標準化を進めることで、スムーズに導入できます。
品質と効率を両立させるために、今こそ自社の業務を見直し、標準化の取り組みを進めてみてはいかがでしょうか。