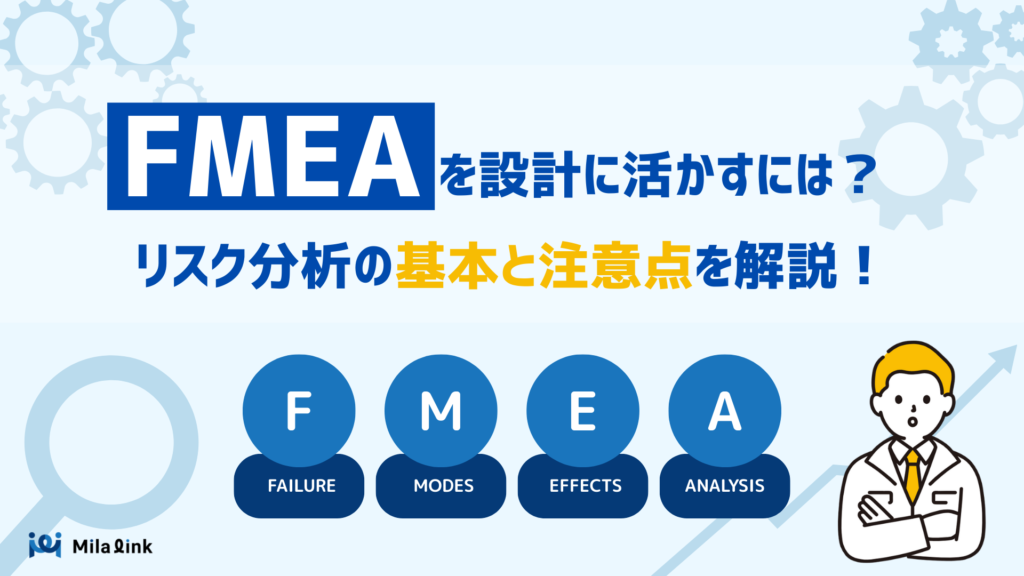
製品開発の現場で、いかに初期段階からリスクを把握し、設計品質を高められるか。
それは、製造業における競争力を左右する大きな要素です。
特に近年は製品の複雑化に伴い、設計フェーズでの不具合未然防止の重要性が増しています。
こうした背景の中で注目されているのが、FMEA(故障モード影響解析)という手法です。
FMEAは設計者自身が不具合の発生パターンとその影響を事前に洗い出し、設計変更や対策を講じるための体系的な思考プロセスです。製造ラインや検査でトラブルを検出するよりも、設計段階で“防ぐ”という発想を実現するための基盤となります。
設計FMEAとは?工程FMEA・システムFMEAとの違い
FMEAには用途に応じていくつかの種類があり、それぞれの目的に応じて適用範囲や分析の視点が異なります。設計部門が最も頻繁に活用するのが「設計FMEA(DFMEA)」です。
設計FMEAでは、製品の構造や機能、仕様に対して「どのような不具合が起こりうるか」「それがどんな影響を及ぼすか」を予測し、事前に対策を講じることを目的としています。たとえば、部品の形状や材質に起因する破損リスク、使用環境による動作不良といった、設計者が主導して対処できる課題が対象になります。
これに対し、「工程FMEA(PFMEA)」は製造現場での工程を対象とした手法です。具体的には、組立ミス、加工不良、測定ミスなど、生産現場で発生する可能性のあるエラーを想定し、工程設計や作業手順に反映していくために活用されます。PFMEAは、生産技術や品質保証など製造寄りの部門が主体となって実施するのが一般的です。
また、「システムFMEA」は、複数の機能や構成部品が組み合わさって構成されるシステム全体を対象とした分析です。電子制御ユニット(ECU)や安全機構を含むような製品では、各要素が相互にどのように影響を与え合うかを考慮する必要があります。システムFMEAでは、単体では問題がなくても、組み合わせによって起きる誤作動や相互干渉といったリスクを洗い出すことが目的です。
このように、設計FMEAは「部品・構造・機能の不具合予防」に焦点を当てるのに対し、工程FMEAは「製造中のミスや不良防止」、システムFMEAは「システム全体の整合性と安全性」を対象とするという違いがあります。それぞれのFMEAは開発段階に応じて使い分けられ、全体として一貫性のある品質保証体制を築くための重要な役割を担っています。
🔧 設計FMEA(DFMEA)
- 対象: 製品の構造・機能・仕様
- タイミング: 設計初期〜試作段階
- 分析単位: 構成部品・機能単位
- 目的: 設計段階での不具合予測とリスク低減
- リスク例: 強度不足、誤仕様、誤機能
- 利用者: 設計エンジニア
🏭 工程FMEA(PFMEA)
- 対象: 製造工程(作業・設備)
- タイミング: 量産準備・工程設計時
- 分析単位: 作業・工程ステップ単位
- 目的: 製造不良の未然防止
- リスク例: 作業ミス、設備トラブル、不良品流出
- 利用者: 生産技術者、製造エンジニア
🧩 システムFMEA
- 対象: システム全体(構成要素の連携・相互作用)
- タイミング: 構想・上流設計段階
- 分析単位: サブシステム・機能ブロック単位
- 目的: 全体整合性と誤作動の防止
- リスク例: 信号干渉、相互作用ミス、冗長性の欠如
- 利用者: システム設計者、PM
DRBFMとの関係:設計変更に強いFMEA応用手法
近年、FMEAの拡張手法として注目されているのが「DRBFM(Design Review Based on Failure Mode)」です。これはトヨタ自動車が提唱した手法で、設計変更によって発生するリスクに特化して分析するものです。
DRBFMは「変化があるところにリスクあり」という思想に基づいており、小さな設計変更であってもそれに伴う影響を徹底的に議論し、見逃しを防ぎます。FMEAの網羅的な分析に対し、DRBFMはより深く、集中的なレビューに特化しています。
設計変更が頻繁なプロジェクトや、新旧製品の派生モデル開発などでは、DRBFMの活用が特に有効とされています。
FMEAを効果的に活用するための実施ステップ
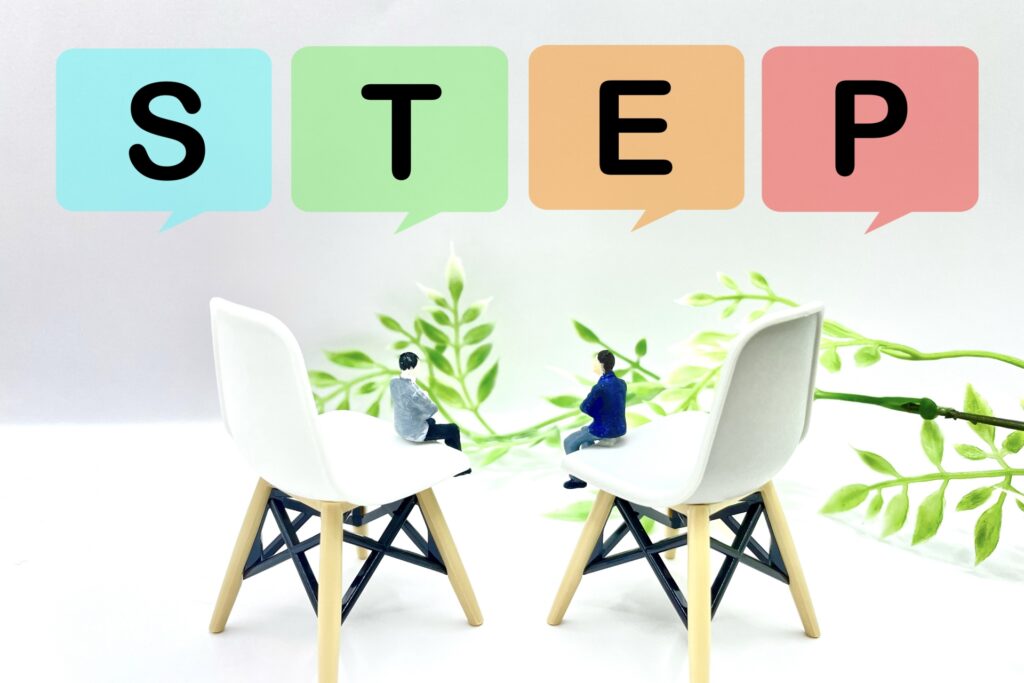
FMEAを有効なリスク分析ツールとして機能させるためには、単に様式を埋めるのではなく、論理的かつチーム主導でのプロセスに基づいた実施が不可欠です。特に設計段階でのFMEA(DFMEA)においては、以下のステップに沿って進めることで、漏れや曖昧さを最小限に抑え、具体的な改善へとつなげることができます。
- 対象範囲の明確化
まず最初に行うべきは、FMEAの対象とする構成品や機能、システムの明確化です。どこまでを分析対象とするかを曖昧にしたまま進めると、不要に広範囲になって作業が膨大になる一方で、重要な箇所を見落とすリスクもあります。 - 潜在的な故障モードの抽出
対象が定まったら、設計や仕様から考えられる「起こりうる故障モード(不具合の形態)」を洗い出します。ここでは過去の不具合情報や他製品の事例、現場のヒアリングが有用です。実際のトラブル事例を挙げながら具体的に検討することが、信頼性のある分析につながります。 - 故障の影響評価(重篤度)
各故障モードが発生した場合に、それが製品やユーザーにどのような影響を及ぼすかを評価します。安全性、機能喪失、ユーザーの不満など、影響の深刻度を定量的にスコア化します(通常は10段階)。 - 発生度と検出度の評価
次に、その故障がどの程度の頻度で起こり得るか(発生度)、また起こった場合にどれほどの確率で検出できるか(検出度)を評価します。これらも経験やデータに基づいて判断し、ばらつきを避けるためにチームでの合意形成が求められます。 - リスク優先数(RPN)の算出と優先順位付け
「重篤度 × 発生度 × 検出度」によってリスク優先数(RPN)を算出し、優先度の高いリスクを特定します。すべての故障モードに対策を講じるのではなく、RPNが高いものに絞って集中的に対応するのがポイントです。 - 対策の立案と再評価
このプロセス全体を、設計者だけで完結させるのではなく、品質保証、生産技術、調達、サービス部門など多様な視点を持つメンバーとともに進めることが極めて重要です。現場の知見が反映されたFMEAは、より実用性の高いリスク分析となり、最終的なトラブルの未然防止と設計コストの節約に繋がります。
FMEAの限界とその対策
FMEAは不具合未然防止に有効な手法ですが、限界もあります。特に、経験や記憶に依存する性質上、「知らないこと」や「記録されていない過去のトラブル」は分析対象から漏れてしまう可能性があります。
これに対応するためには、FMEA単体ではなく、以下のような組織的なサポートが不可欠です。
- 不具合データベースの構築と活用
- テンプレートや過去事例の共有による抜け漏れ防止
- ナレッジ管理ツールによる知見の蓄積
- 若手教育やレビュー会の継続による技術継承
さらに最近では、設計AIエージェントの導入も注目されています。たとえば、ミラリンクが提供する「タグっと」のようなツールは、過去の設計事例や不具合情報をAIが自動で解析・関連付けし、設計中に類似ケースを提案してくれる機能を持っています。これにより、担当者が知らなかった過去の事例や見落としがちなリスクにも気づけるようになり、FMEAの精度を高めることが可能になります。
FMEAは「考えること」が本質です。その考察を深めるためには、過去の知見を組織全体で支える仕組みづくりに加え、AIのような新しい技術を柔軟に取り入れる姿勢も重要です。人とツールが補完し合う体制を整えることで、より質の高い設計リスクマネジメントが実現できるでしょう。
まとめ:FMEAを設計現場で活かすために必要な視点
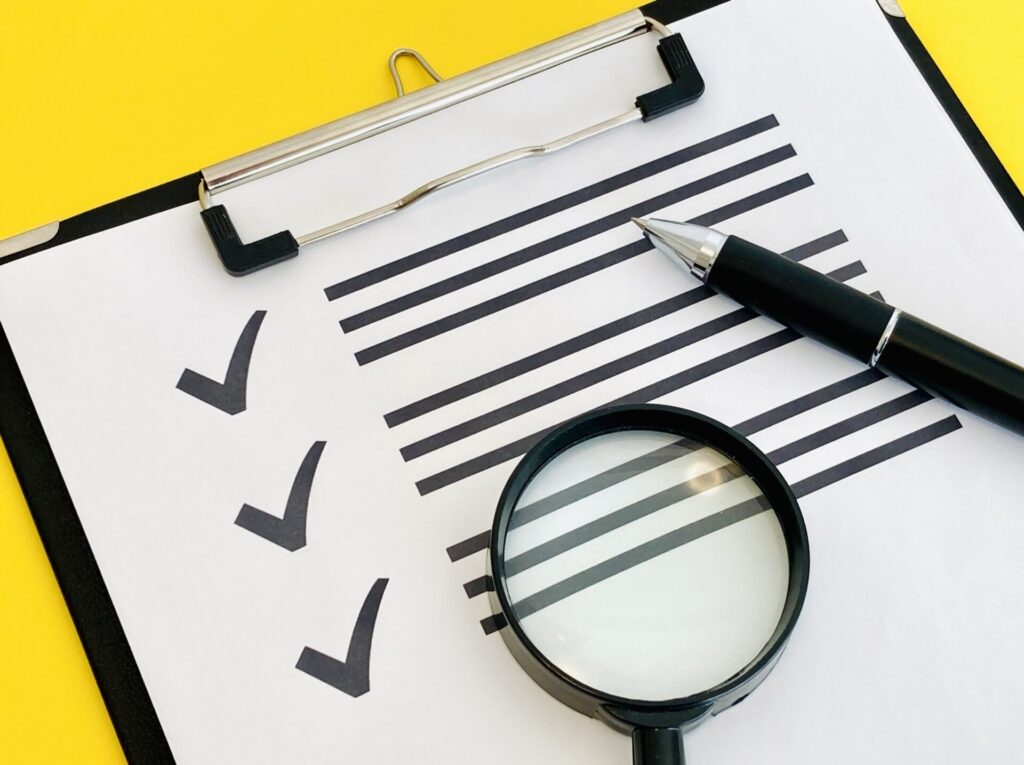
FMEAは、設計段階から製品の信頼性や安全性を確保するための中核的な手法です。しかし、本質は“記入すること”ではなく、“考えること”にあります。単なる形式作業として実施していては、その効果は限定的です。設計者が自らの手でリスクを想像し、「なぜ失敗が起きるのか」「どうすれば防げるのか」を深く考え、チームで共有・議論するプロセスこそが、FMEAの最大の価値です。
また、FMEAは他の手法と組み合わせることで、より実効性の高いリスク分析が可能になります。FTAによる原因追跡、DRBFMによる設計変更点の深堀り、さらにはAIエージェントによる過去事例の活用など、多角的なアプローチが求められる時代です。
今後、製品の複雑化や開発スピードの加速が進む中で、FMEAの役割はますます重要になります。そのためにも、FMEAを“ツール”としてだけでなく、“設計思想の一部”として捉え直す視点が求められます。あなた自身の業務でも、「この設計は本当に安全か?」「見落としはないか?」という問いを持ち続けることが、より良いモノづくりへの第一歩となるはずです。