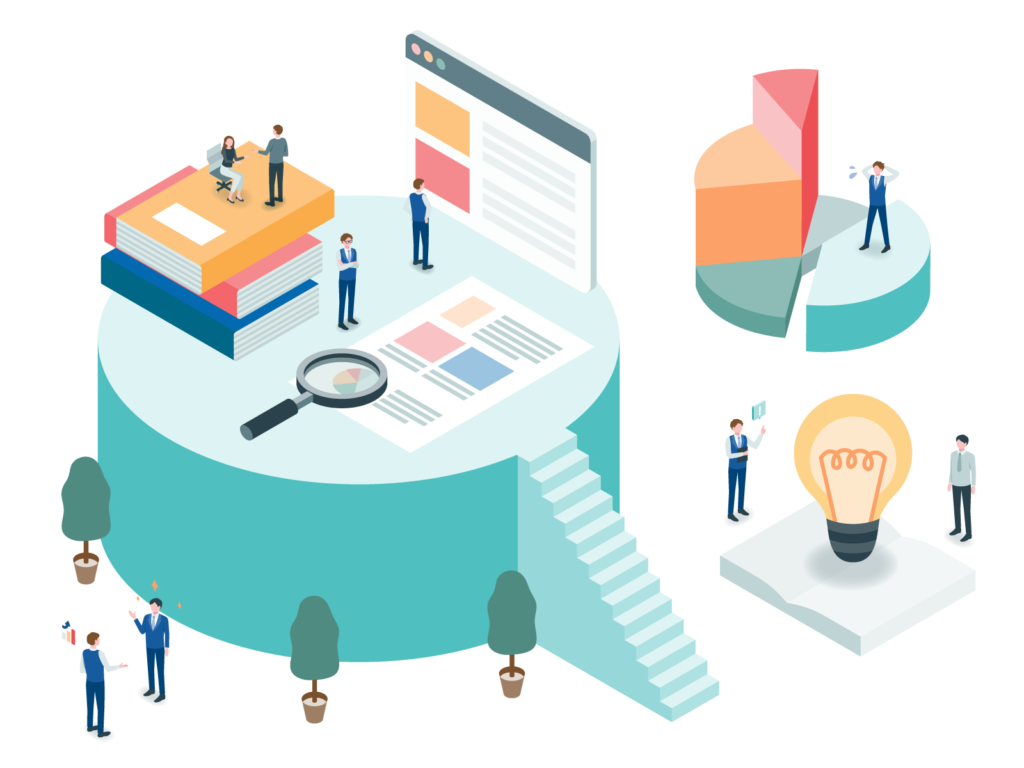
製造現場において、業務の効率を上げるためには、現状の問題点を正確に把握し、適切な改善策を講じることが不可欠です。しかし、現場の状況が見えづらいと、課題を特定するのに時間がかかり、改善の効果も限定的になってしまいます。
そこで重要になるのが 「見える化」 です。生産状況や品質管理、設備の稼働率などを可視化することで、ボトルネックやムダを発見しやすくなり、効率的な改善が可能になります。
本記事では、製造現場における「見える化」の基本から、具体的な導入方法、実践ポイントまで詳しく解説します。
見える化とは?製造現場における重要性
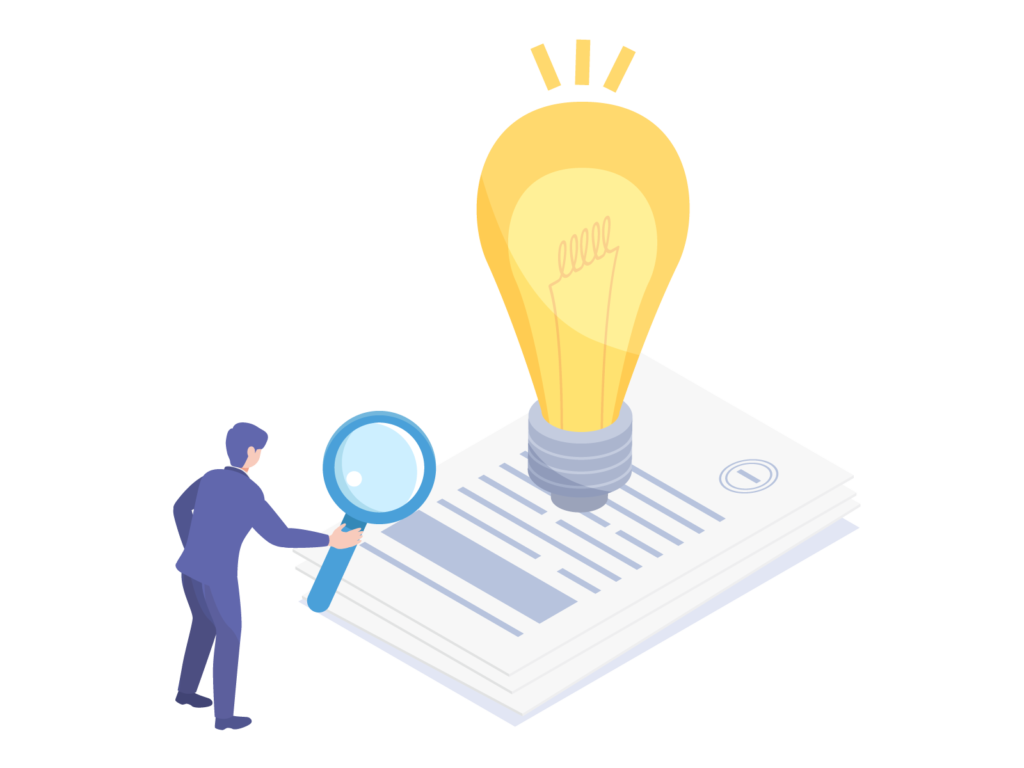
見える化とは、業務の進捗や課題を 目に見える形 にすることで、問題点を素早く把握し、迅速に改善を行うための手法です。製造業では、以下のような分野で見える化が活用されています。
- 生産の見える化
- 進捗状況や生産ラインの稼働率をリアルタイムで把握
- 品質の見える化
- 不良品の発生状況やその原因を可視化し、品質改善を促進
- コストの見える化
- 材料費や人件費のデータを整理し、コスト削減のポイントを特定
- 設備の見える化
- 機械の稼働状況やメンテナンスの必要性をリアルタイムで管理
このように、見える化を行うことで、これまで「なんとなく問題がありそう」と思っていたことが 数値やデータとして明確になり、的確な改善につなげることができます。
見える化のメリット
製造現場で見える化を実践すると、以下のようなメリットが得られます。
1. 現場の問題点を早期に発見できる
製造工程の情報をリアルタイムで把握できるため、不具合やトラブルの発生を素早く察知できます。例えば、生産ラインの停止回数が増えている場合、その原因を特定し、未然に防ぐことが可能です。
2. 生産性が向上する
作業者の動線や工程のムダを可視化することで、不要な手順や待ち時間を削減できます。これにより、スムーズな生産フローを実現し、作業効率を向上させることができます。
3. 品質の向上
不良品の発生率や発生場所をデータ化することで、品質管理がしやすくなります。例えば、不良品の原因が「材料のばらつき」にあるのか「作業ミス」にあるのかを特定し、的確な対策を講じることができます。
4. コスト削減につながる
生産ラインのムダな工程や過剰な在庫を可視化することで、無駄なコストを削減できます。また、機械の稼働データを分析し、適切なメンテナンスを行うことで、設備の故障を防ぎ、修理コストの削減にもつながります。
5. 現場の意識改革が進む
データが共有されることで、作業者の意識が変わり、全員が「改善すべき点」を意識するようになります。現場主導での改善活動が活発化し、継続的な効率向上につながります。
見える化を実践するためのポイント
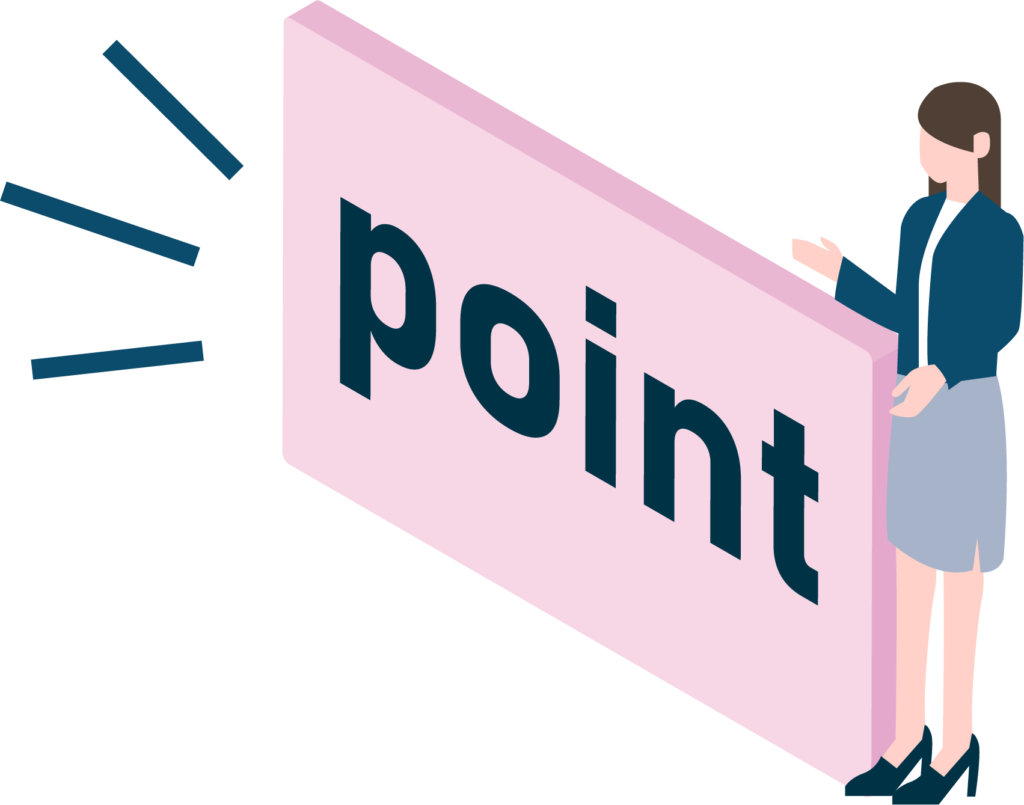
見える化を成功させるためには、適切な手法を選び、現場に定着させることが重要です。以下のポイントを押さえて進めていきましょう。
1. 可視化する対象を明確にする
まず、何を見える化するのかを明確にします。例えば、「生産効率を上げたい」「不良品を減らしたい」「設備の稼働率を上げたい」など、課題に応じて重点的に可視化すべき指標を決めます。
例:見える化の対象とする指標
- 生産ラインの稼働率
- 作業時間(待ち時間や非効率な動作の有無)
- 不良品率
- 設備の停止回数とその原因
2. データを活用しやすい形で整理する
収集したデータを、現場の人が 直感的に理解できる形 に整理することが重要です。例えば、グラフやチャートを活用したり、色分けして視覚的に分かりやすくすることで、誰でも簡単に問題を把握できるようになります。
3. リアルタイムで情報共有する
データを収集しても、それが現場で活用されなければ意味がありません。デジタルツールやダッシュボードを活用し、リアルタイムで情報を共有することで、素早い判断が可能になります。
活用例
- デジタルサイネージ を導入し、生産状況や進捗をリアルタイムで表示
- IoTセンサー を活用し、設備の稼働データを自動収集
- クラウドシステム を使い、作業者や管理者がいつでもデータを確認できるようにする
4. 見える化したデータを基に改善策を実行
見える化は、あくまで「現状を把握する手段」であり、最終的な目的は「改善」です。データを分析し、具体的な改善アクションを設定することが重要です。
例えば、不良品が特定の工程で多く発生している場合、作業手順を見直したり、作業者の教育を強化するなどの対策を講じます。
5. 現場の負担を増やさない工夫をする
見える化を導入する際、現場の作業者に過度な負担がかかると、定着しにくくなります。そのため、可能な限り 自動でデータ収集できる仕組み を取り入れたり、簡単に入力できるシステムを採用することが重要です。
見える化の成功事例
事例1:製造ラインの稼働率向上
ある工場では、生産ラインの稼働率が低いことが課題でした。IoTセンサーを活用して各機械の稼働状況をリアルタイムで監視し、停止の原因を分析したところ、「段取り替えの時間が長い」ことが判明。作業手順の見直しと人員配置の最適化により、稼働率を~~15%~~向上させることができました。
事例2:不良品の削減
別の工場では、不良品率が高く、原因が不明でした。作業ごとの検査データを見える化した結果、特定の時間帯に不良率が高くなることが判明。詳細な分析を行ったところ、作業者の疲労によるミスが原因だったため、休憩時間を適切に設定し、不良率を~~30%~~削減しました。
まとめ
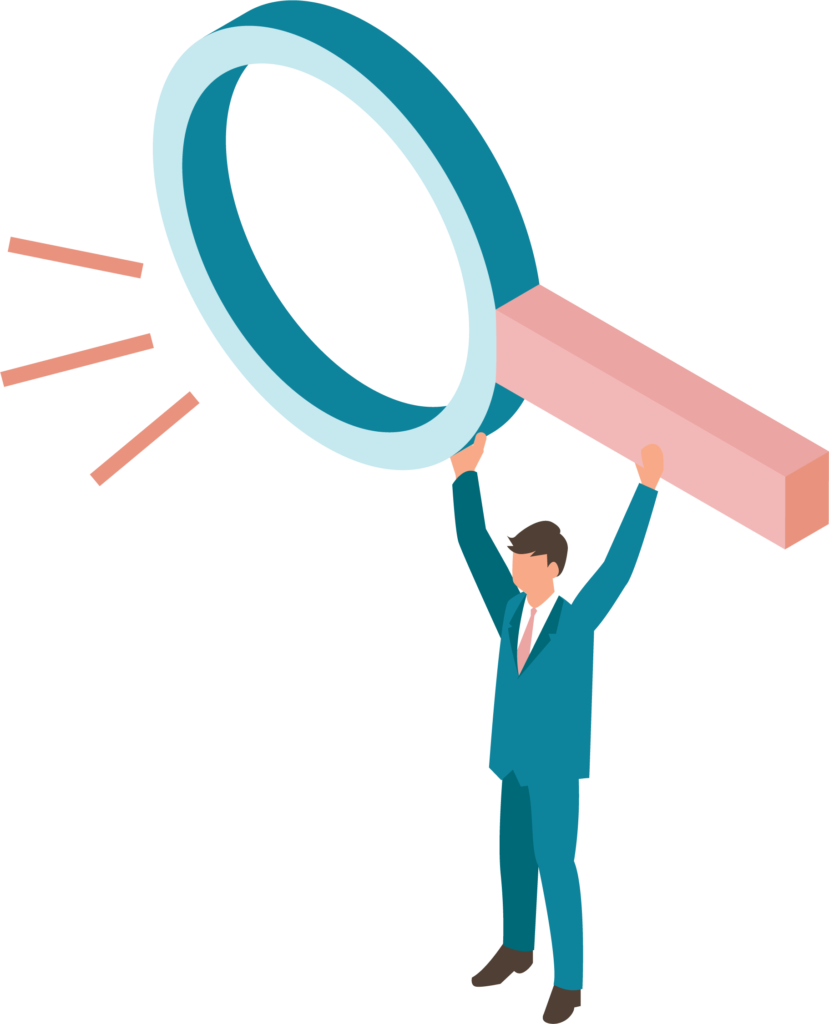
製造現場の「見える化」は、業務の効率化や品質向上、コスト削減に大きく貢献します。適切な指標を設定し、データをリアルタイムで共有・活用することで、具体的な改善につなげることができます。
現場の課題を可視化し、改善のサイクルを回すことで、継続的な生産性向上を実現していきましょう。